Not many villages have any particular feature that would make them stand out. But the villages Savran, Osychky, and Vilshanka in Podillia have their own specialty: making wicker brooms, or “vinyky.” Locals call such brooms environmentally friendly hoovers. Here, as well as in several other locations in different regions, wicker brooms are made for all of Ukraine. Sown in spring and harvested in late summer, millet, which is used for making the brooms, “feeds” the villages for the whole year.
Everyone weaves wicker brooms here. Children, youth, adults, and seniors are all involved in making them. There is a Ukrainian saying that goes, “A vinyk appeared for rubbish”. However, they are used not only for cleaning but also for spraying flowers, in a home sanctifying ceremony, and more.
Just half a century ago, wicker brooms manufactured in Podillia were sold all over the Soviet Union. Nowadays, they are mostly made for the Ukrainian market. The closest big city is Odesa. Locals take wicker brooms and wicker amulets there to sell. They are sold at the markets, from where they are then brought to many other parts of Ukraine.
There is also a local market in the village Savran. It opens at seven in the morning, and visitors have to buy everything they have come for in less than an hour, or they will run out of time. The market closes very quickly. Wicker brooms are not sold by the piece but in packs of 50. The lifespan of such wicker brooms is one to two years.
Technology of manufacturing
Brooms that are sold are mostly made of proso millet or sorghum stems. However, brooms can be weaved even with stems of bushes, as long as they are dried. Before, these hastily made brooms often were found in village homes.
In Savran and nearby villages, brooms are weaved with proso millet stems. This crop grows well in local soils, so the harvest is abundant.
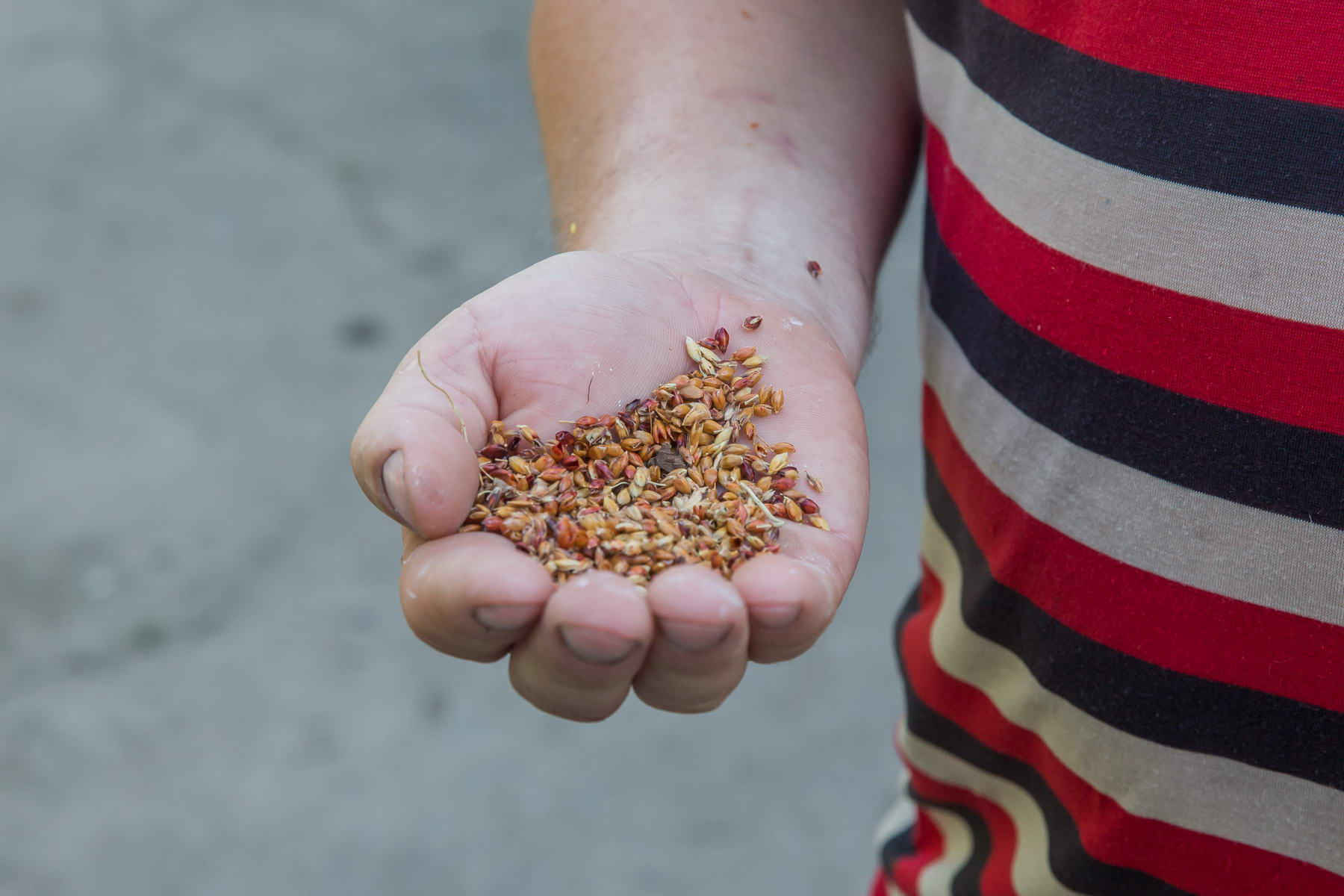
The broom-making process starts long before the craftsman sits down to weave it. To start, proso millet is sown at the end of April or beginning of May, to then be hoed several times until being harvested in August. Millet is cut, dried, put in yaskas (hammocks for carrying millet — ed.), and brought home. The next step is to clean out the seeds. It takes about a month to process millet harvested from one hectare, and in the end about 2,000 brooms are made of it. Millet stems are bound together and put in three bundles, and only after that actual weaving of the broom starts.
It usually takes an experienced craftsman just five minutes to weave one broom. However, everything depends on the person and his or her temperament and work speed.
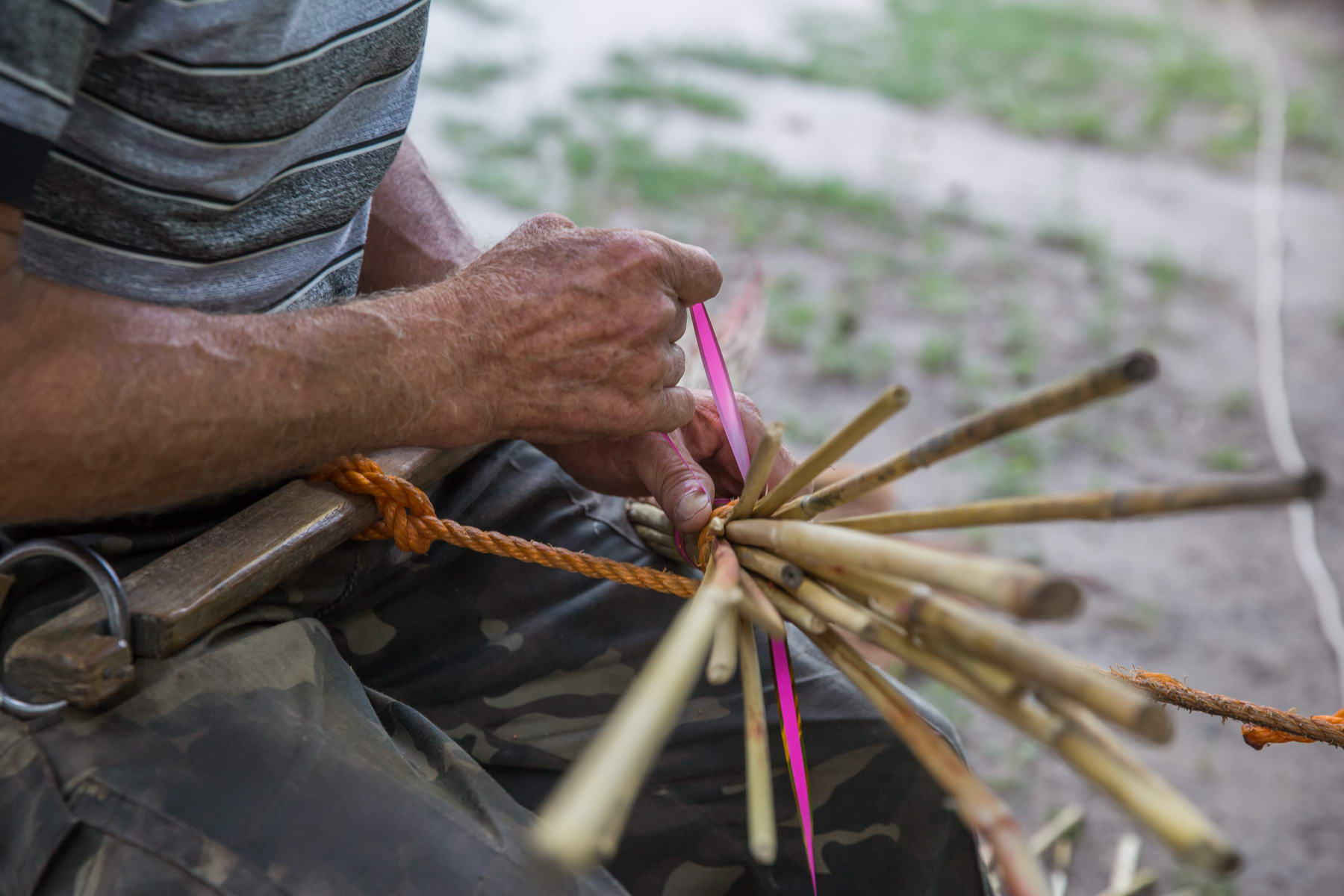
The broom is tied with a special rope — it is handmade especially for this. About 10 years ago, brooms could be tied with vine, but today such items do not sell well, so broom weavers are asked to use rope. It is said that vine cracks in dry and hot weather, which also breaks the broom.
To start, a “doll” is woven: three bundles of stems are secured together with the rope. After that, the broom is wound up with the rope. Three times at the base, to shape the broom correctly, and then four more times to form the handle. The doll should be cut at the top, to make it comfortable to hold the broom by hand. Gift brooms are also decorated with golden ribbon above the rope. Smaller brooms serve as amulets at home.
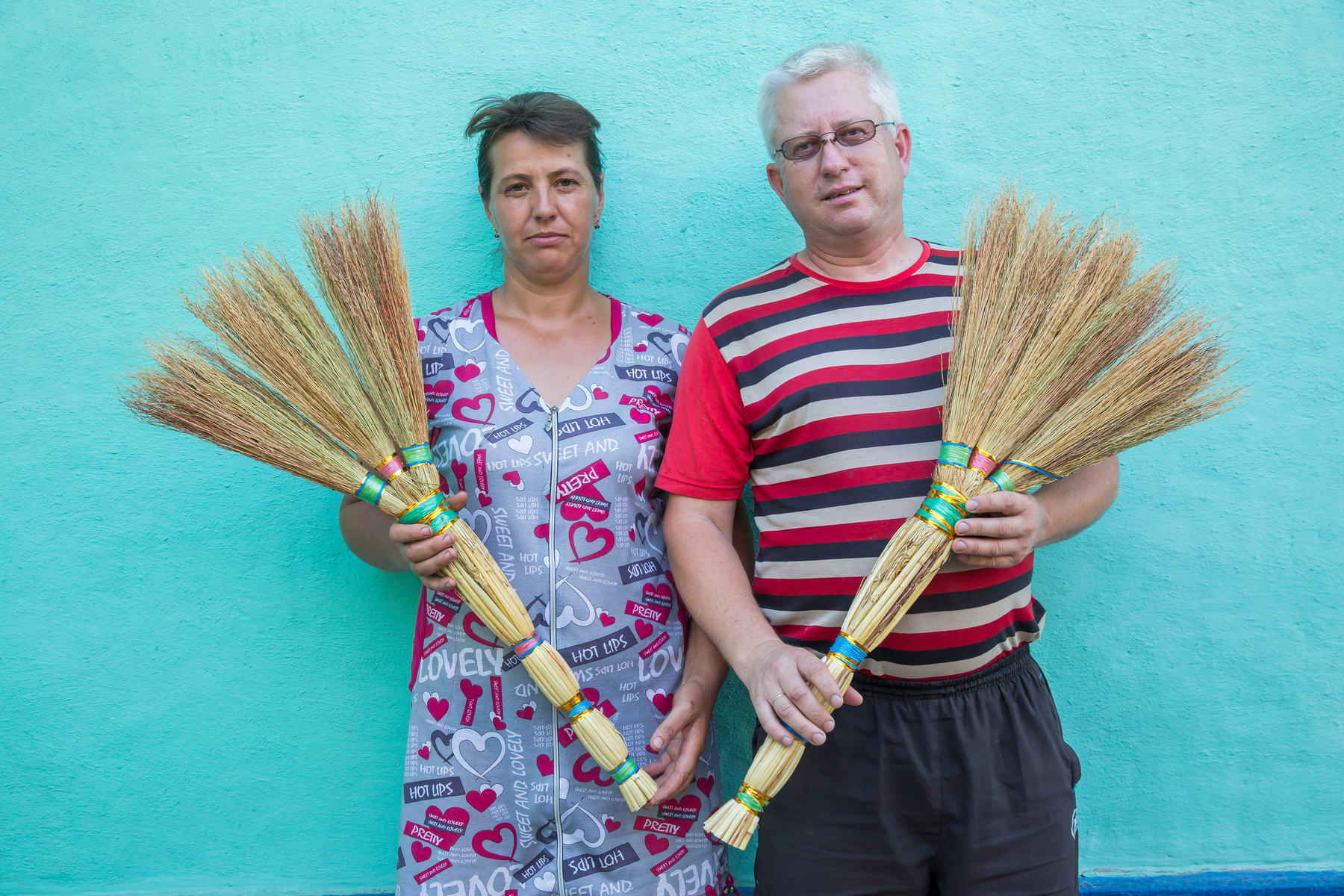
Vasyl and Tetiana
Vasyl Hudz from the village Vilshanka has been weaving brooms since he was little. He remembers his parents promising to give him a coin or to let him go play if he cleaned the proso millet. Later, boys themselves started competing in their craftsmanship: the one who would make the most bundles became cooler than the others. Vasyl made his first broom in the eighth grade. In the beginning, he could not get it right without making mistakes.
— To be honest, it was bad. The first broom is never good. I was trying: I was making one, then two and three at a time.
Vasyl has been living with his wife Tetiana for 20 years and weaving brooms for 30. His parents and grandparents wove brooms, and most likely his children will weave, too:
— Willy-nilly, you have to weave, as you need something to live on.
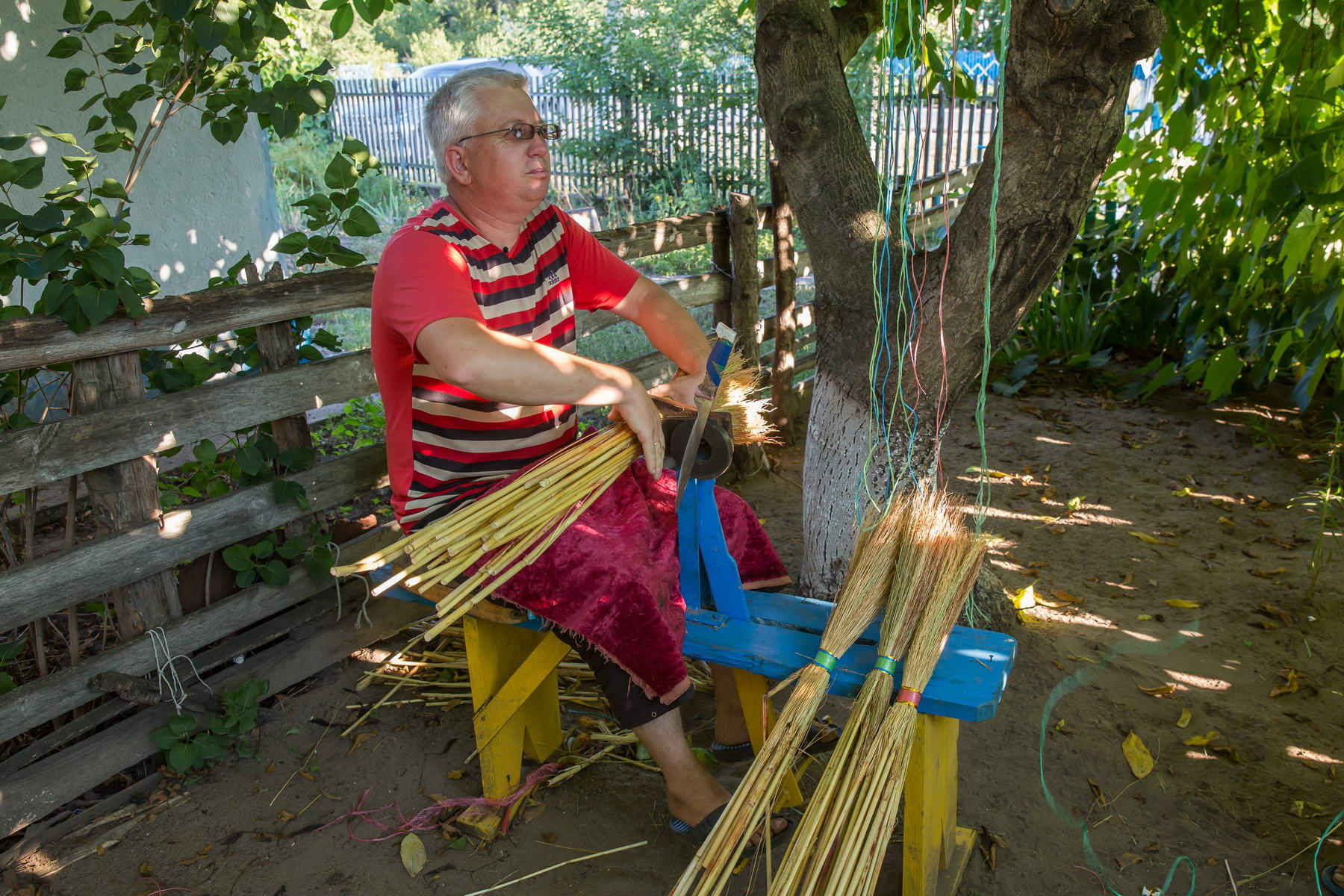
Vasyl has a workshop set up in his backyard. The machine for weaving brooms has a special opening for millet. Millet is compressed under pressure, and it shrinks. Tied to the tree, there are ropes for winding the broom and ribbons for the gift brooms.
He says August is the most difficult time for a broom weaver. It is the time to harvest proso millet, cut it, put it in piles, and clean it. Now and then they work from morning until night to get everything done in time.
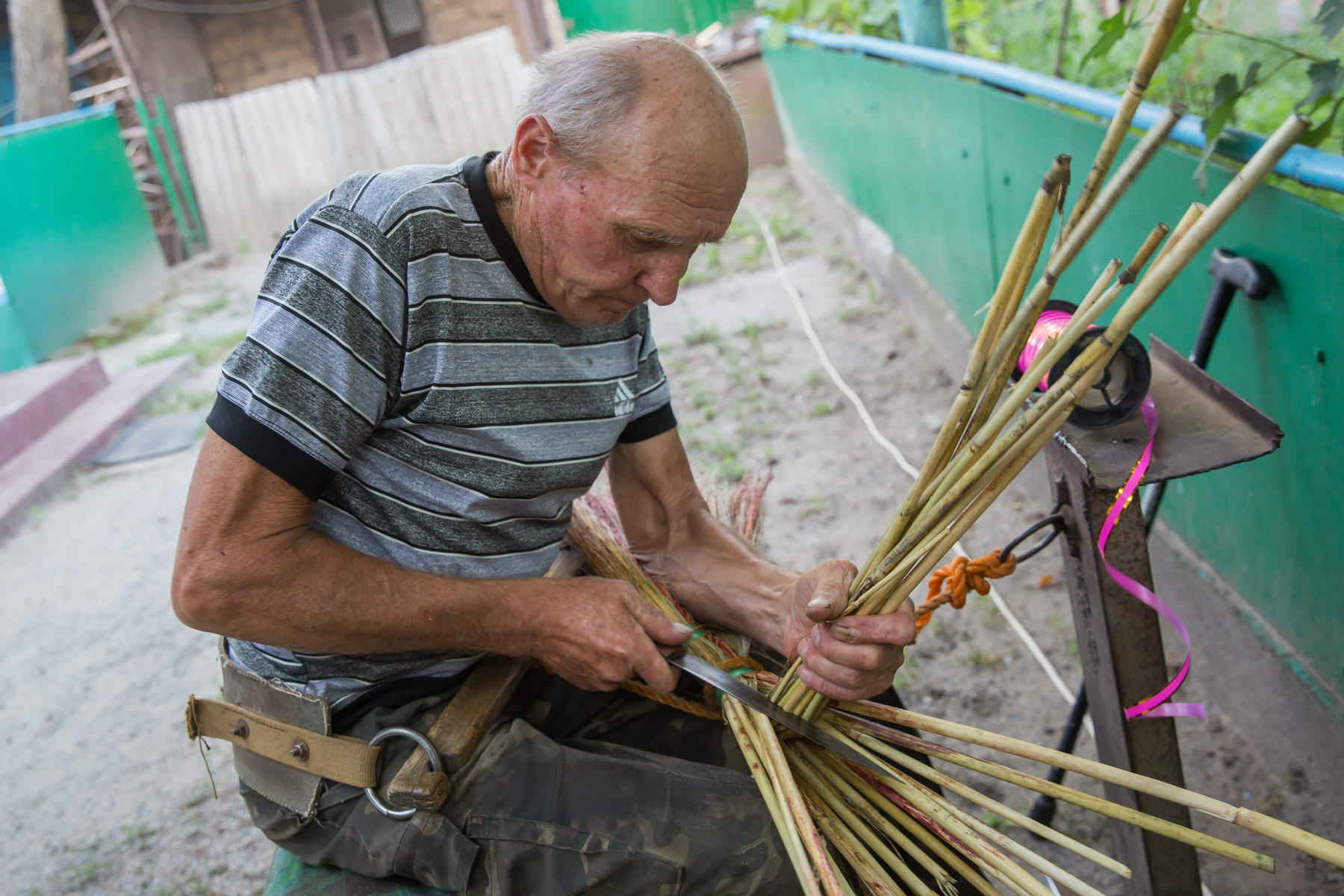
Mykola
Mykola Shpytko from the village Osychky explains how they started making brooms after World War II. It was back then that they sowed proso millet for the first time and weaved the first broom. Today, there are tools for weaving brooms in every yard in Osychky.
Mykola’s parents didn’t make brooms, so he learned the craft himself — sometimes he’d oversee something at the neighbours, and sometimes he’d ask a hired worker, who was weaving brooms at their house, to share his secret. He sat at the weaving machine for the first time in the fifth grade, and since then, for almost 60 years, he has not parted with millet and rope. In the 1960s, when ice cream cost 14 kopecks, getting five extra kopecks for a broom was not at all a bad side job.
He worked as a welder by day and wove brooms by night. Mykola says he could weave 200 brooms a day when he was young, and nowadays about 50 on average.
Almost nothing has changed in broom weaving technology in the last half-century, except for the price. Among local craftsmen, it has become a tradition for a man to make the “body” of a broom and usually for a woman to decorate it with ribbon.
slideshow
During Soviet Union times, Mykola’s father went to other cities to sell brooms, at first for 50 kopecks, and later the price went up to one ruble. Brooms were mostly bought in Russian cities: Gorky (now Nizhny Novgorod), Bryansk, Leningrad (now Saint Petersburg) and Moscow.
As Mykola finishes weaving, he says:
— That’s our job. I’ve been doing this for seven decades, it will be 70 in three years, and still, thank God, I am weaving brooms.
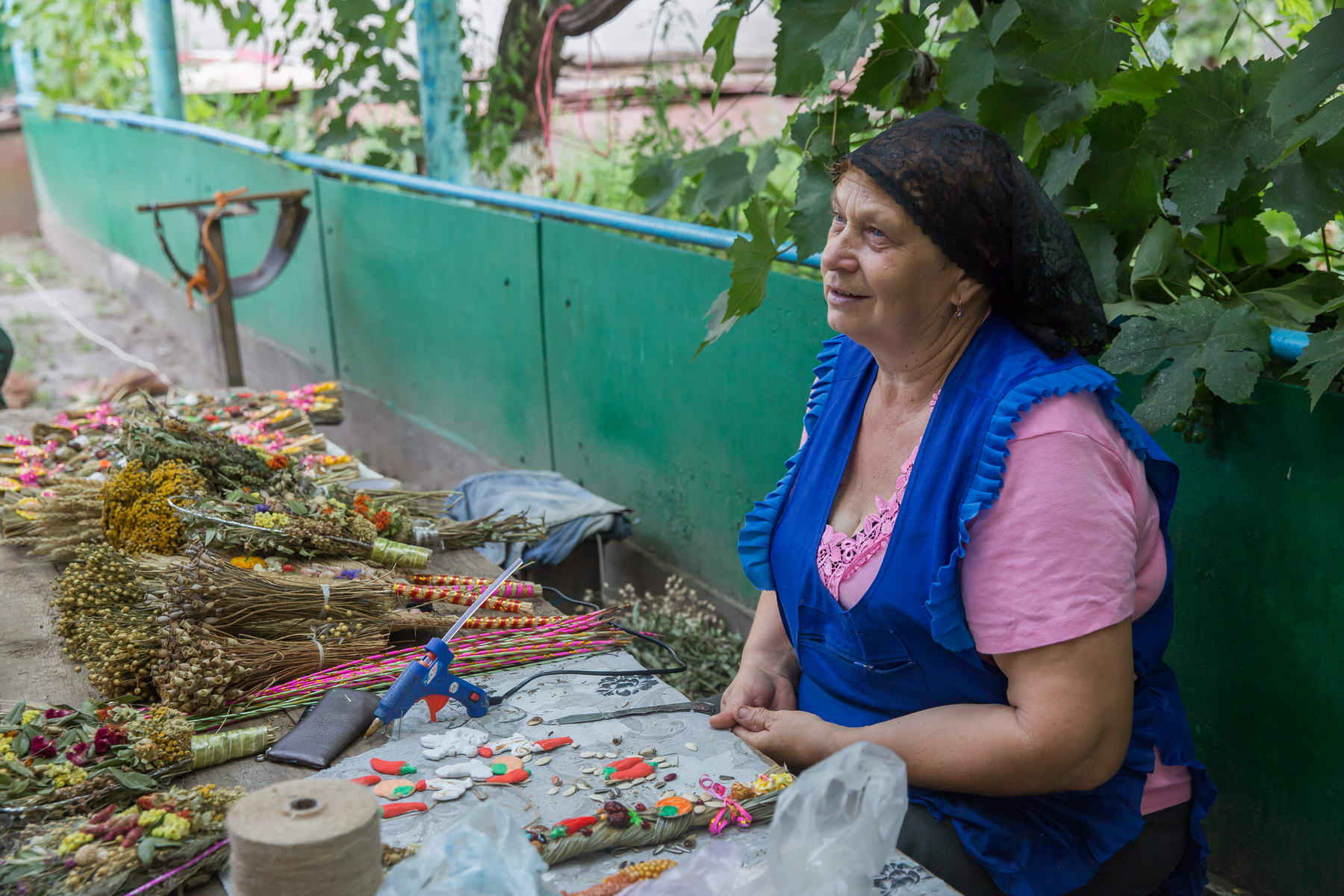
Vira
Vira Shpytko from the village Osychky has been making brooms for many years. She calls herself an entrepreneur — she took her products to Odesa and had her own business. Today she brings handmade amulets to Odesa. She weaves various compositions, in which each component has its own purpose.
— This is the deity who protects the house. Here we see rye, wheat, and oat — to bring the whole family together for festivities. The deity takes all the negative energy in. She comes without eyes – that is done so on purpose.
slideshow
On the Savior of the Honey Feast Day, which is celebrated in mid-August, Vira goes to collect herbs. They are all considered to be healing after sanctification, she says: rye, wheat, saffron, oregano, musk, and yarrow. She dries herbs at first and then weaves braids with them. All decor elements are cast from plaster and painted.
She says the tradition of Shevchenko homes is coming back now. There is a demand for such compositions. So she makes roofs from reed and tiny stones by the entrance from peppers. She learns about the symbolism of herbs on the internet: garlic protects from enemies, and pepper adds on to a man’s dignity.
For locals, weaving brooms is an additional income and a family tradition that has been passed down from generation to generation. They weave during the week and come to sell at the Savran market on Thursdays.
Maybe that broom you have at home is from there.
How we filmed
Watch our visit to the family of broom weavers, see the Savran market — the fastest in Ukraine — and hear about flying brooms in our video blog.