Промислові компанії є одними з найбільших забруднювачів довкілля, тому особливо потребують новітніх чистих технологій. Ця історія — про українські бізнеси, чиї розробки допомагають зменшити вуглецевий слід у металургії. Компанія «Символ» замінює бронзу у виробництві підшипників ковзання на чорний металобрухт і отримує при цьому продукт з більш якісними показниками. А команда підприємства «Червона хвиля» випустила унікальну установку для тривимірного друку надстійким матеріалом — титаном, що активно використовується в авіаційній та космічній галузях.
Метал — один із матеріалів, які найчастіше використовують у сучасному світі. Наш світ збудований з металу: від машин та обладнання до сучасних будівель. Ложка, якою їмо вівсянку та кабель, яким приходить додому інтернет — теж з металу. Україна входить до списку країн із досвідом розробки високотехнологічних металургійних процесів та повним циклом виробництва титану та титановмісних продуктів. Українські металургійні підприємства зосереджені переважно навколо таких великих міст, як Донецьк, Запоріжжя, Дніпро, Кривий Ріг, Маріуполь. З початком російсько-української війни у 2014 році деякі підприємства зі Сходу України були змушені переїхати на підконтрольну Україні територію.
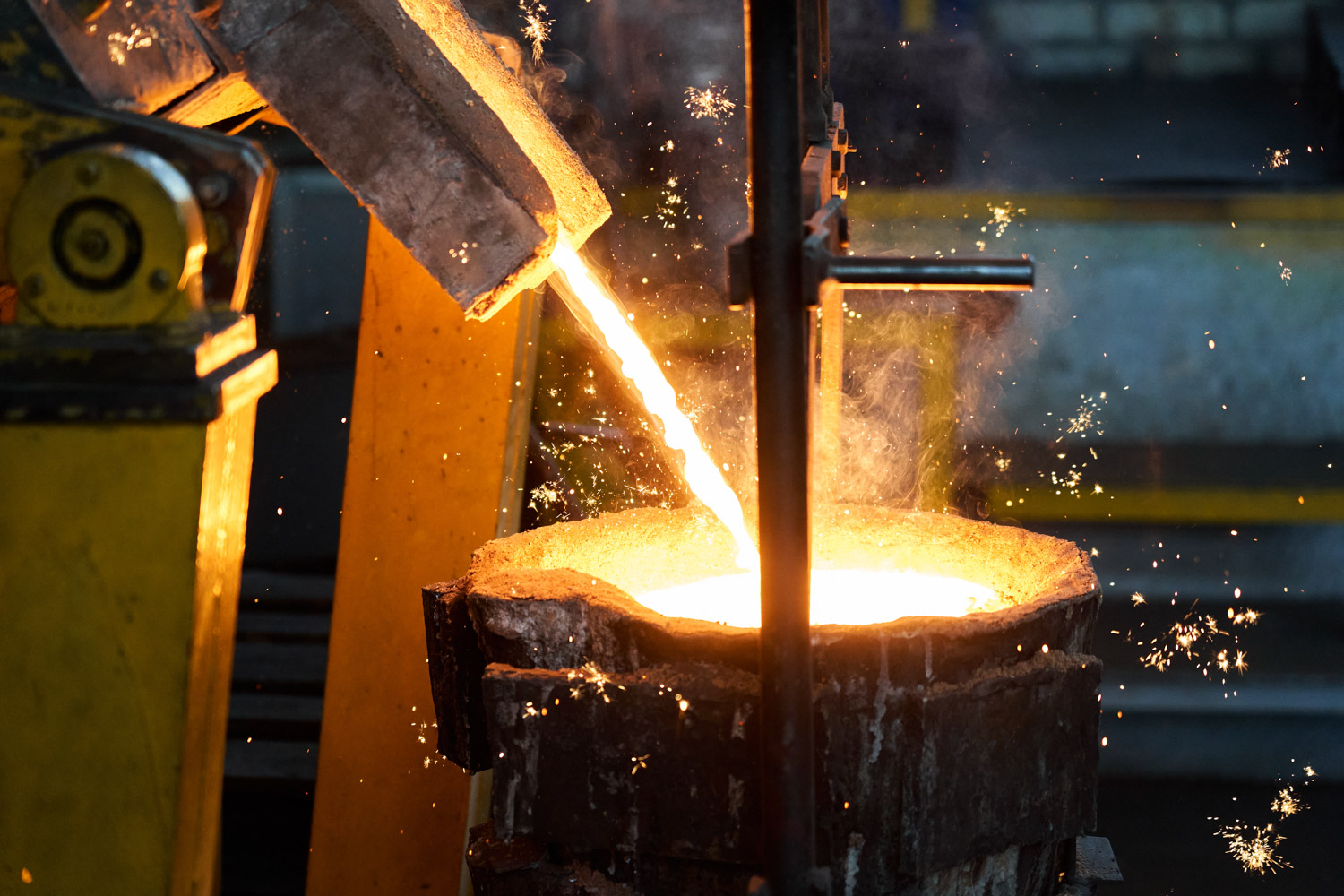
Та металургійні гіганти неабияк забруднюють навколишнє середовище, викидаючи у повітря мільярди тонн вуглекислого газу (СО2). Виробництво чавуну та сталі, алюмінію та титану, міді та бронзи не обходиться без шкідливих викидів у повітря. Зараз світова металургія та металообробка шукає шляхи зменшення масштабів забруднення, рішення, які допоможуть скоротити обсяги відходів та використати їх як сировину для інших виробництв. І тут на допомогу приходять нові технології.
«Символ». Робити підшипники з металобрухту
Металургійна компанія «Символ» виливає деталі зі сплавів різних металів та виготовляє підшипники ковзання, які використовуються в гірничодобувній промисловості, металургії, машинобудівництві, енергетиці тощо.
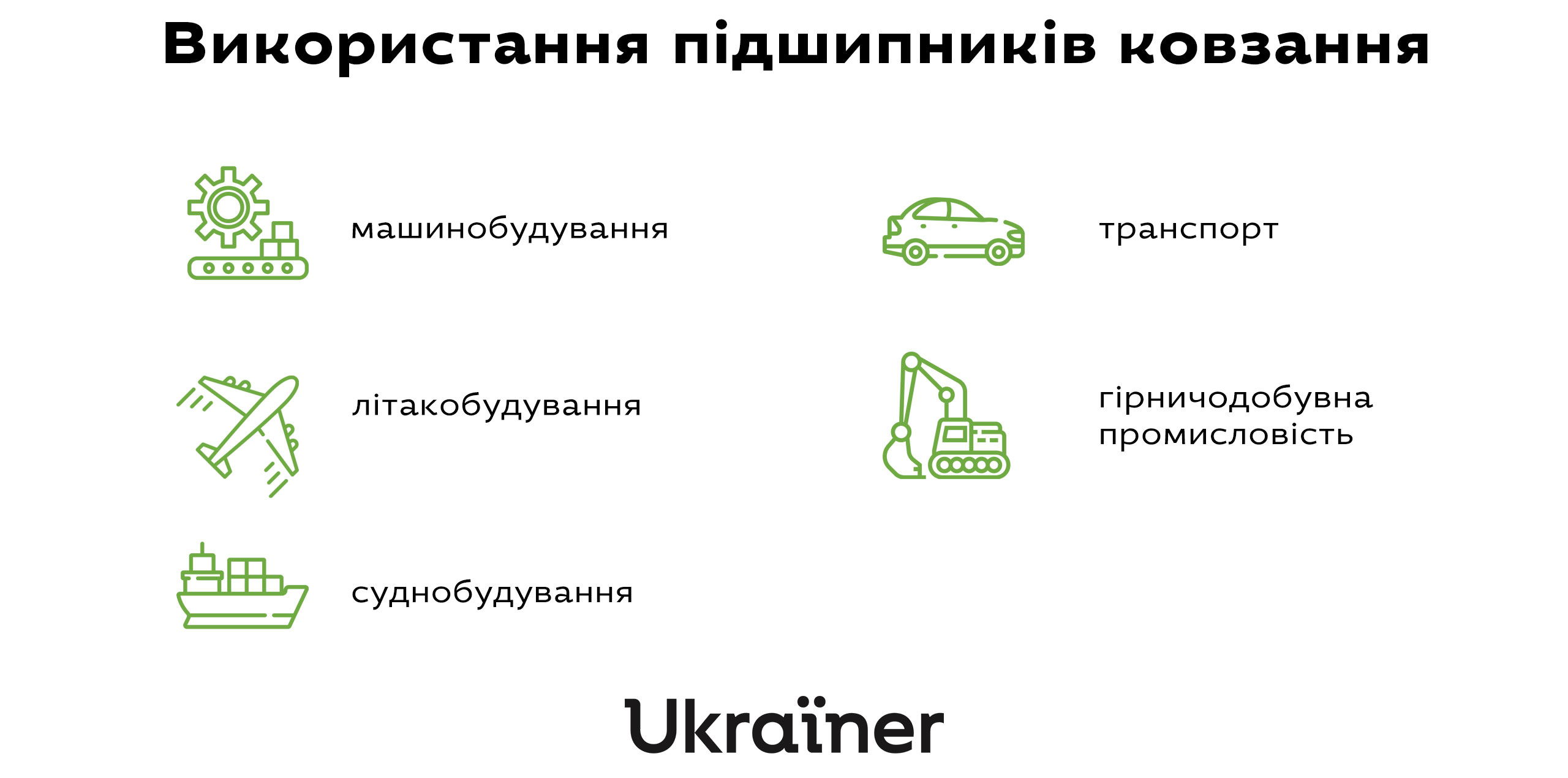
Підшипник ковзання — необхідний елемент багатьох механізмів, що працюють в умовах значних навантажень та агресивних середовищ, де потрібна компактність та тривалий строк служби. Порівняно з більш відомими підшипниками кочення (тими, з яких в дитинстві ми діставали кульки), підшипники ковзання мають набагато простішу конструкцію і краще витримують ударні та вібраційні навантаження. Такі підшипники роблять зокрема, з твердих сплавів, з бронзи, композитних матеріалів (із вмістом пластику) і навіть з твердих сортів дерева. Втім, за словами директора «Символа» Дмитра Акішина, такі підшипники відносно дорогі, а їхнє виробництво завдає шкоди довкіллю.
— Ми хочемо замінити дорогі матеріали на більш дешеві та стійкі. Ці матеріали під назвою АЧМ 200 і є темою нашої роботи.
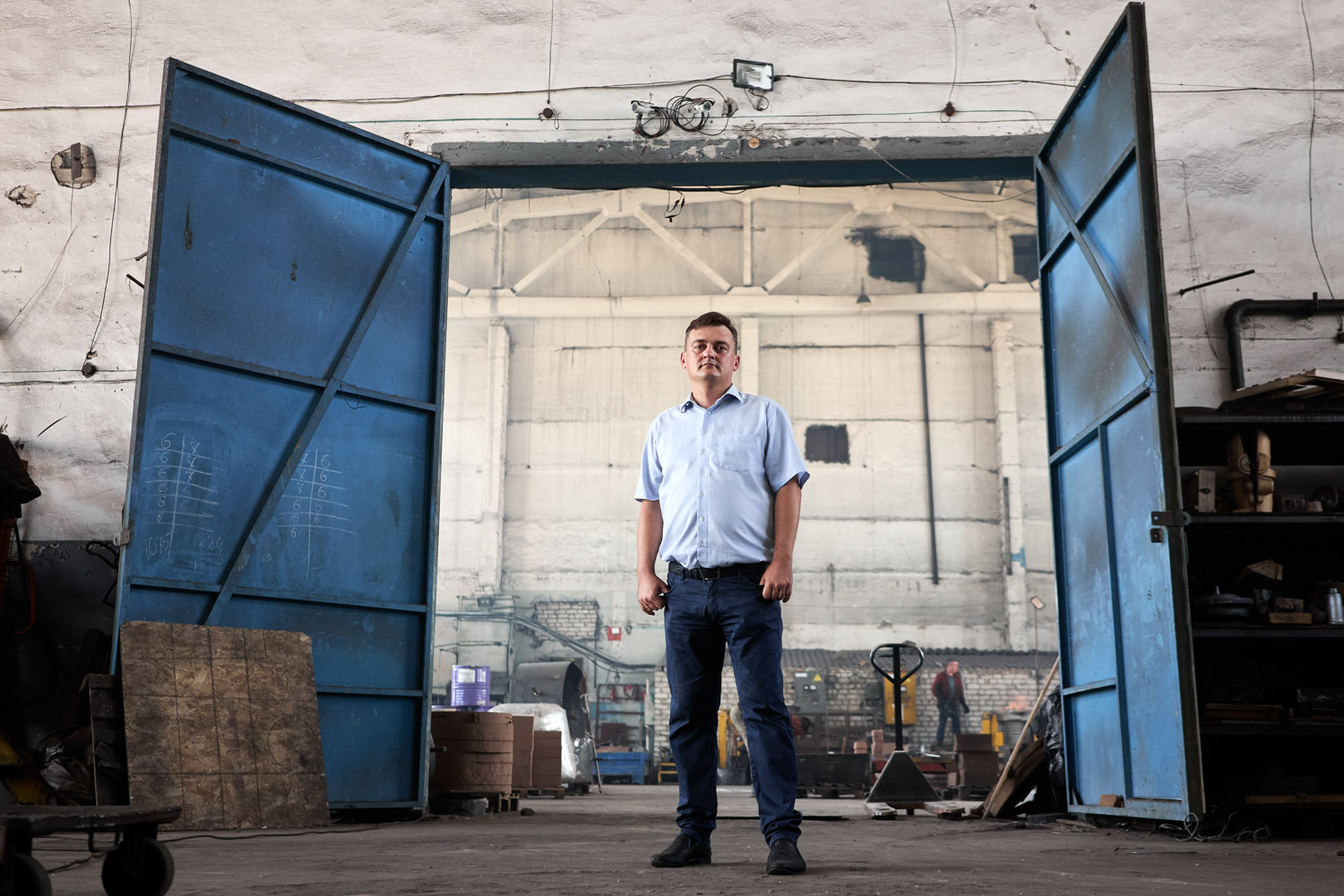
Як виготовляються деталі для механізмів, де задіяні підшипники ковзання? Конструктор на підприємстві розробляє так звану «пару ковзання». Зазвичай це вісь і підшипник. Спершу макет деталі для підшипника виготовляється із пінополістиролу, далі робиться модель із дерева і відливається деталь з металу, яка ще потребує механічної обробки. Врешті готова деталь потрапляє до замовника.
Компанія «Символ» розробила антифрикційний сплав, застосування якого дозволяє виготовити підшипник ковзання з вторсировини — брухту чорних металів. Такий підшипник, за словами Дмитра Акішина, працює довше, наприклад, за бронзовий, витримує більші навантаження й температури.
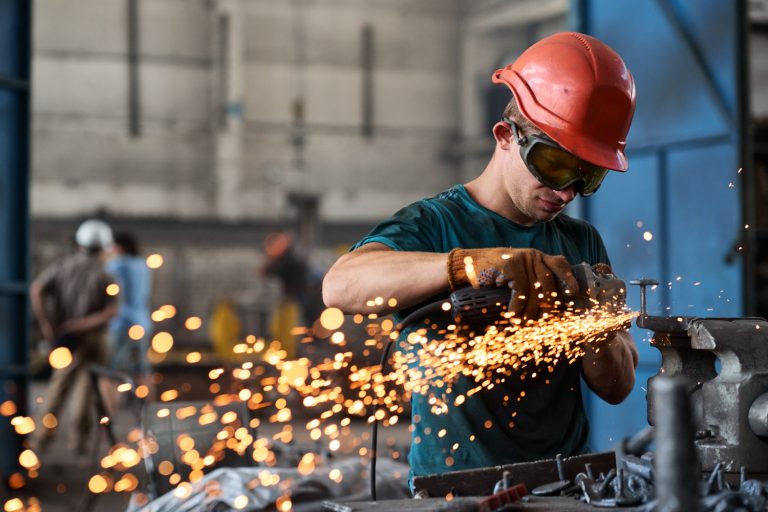
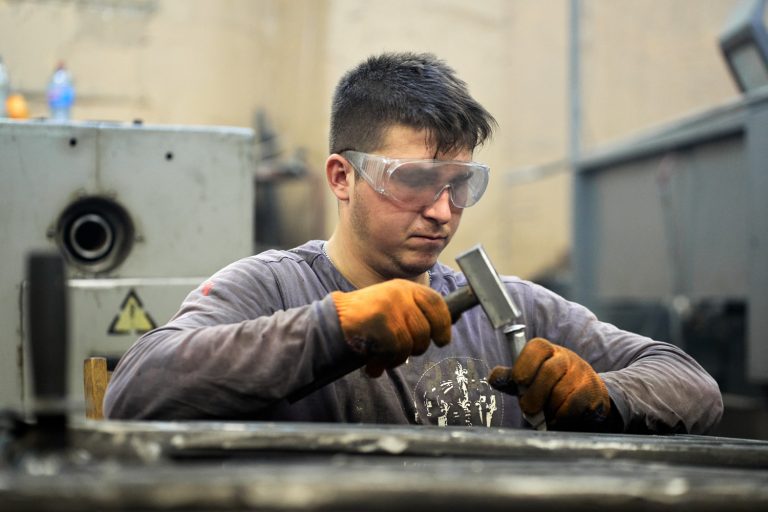
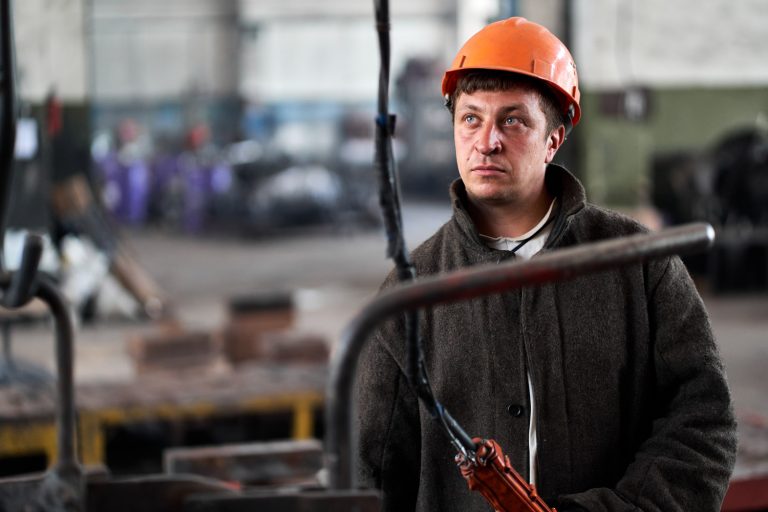
слайдшоу
Чавун і сталь, з яких на 90% складається сплав АЧМ 200 (Антифрикційний чавун модифікований. — ред.), порівняно із тією ж бронзою мають дуже високі антифрикційні властивості. Тобто у виробів з такого сплаву нижчий коефіцієнт тертя при взаємодії з іншими поверхнями, що у виробництві підшипників є критично важливим фактором.
«Символ» почав роботу в 2010 році на Сході України, в Луганську. Та вже за чотири роки вони були змушені зупинити виробництво через російську окупацію регіону. Півтора роки компанія була в законсервованому стані:
— Коли постало питання, що місцеві окупаційні адміністрації мають різати наше обладнання на металолом, ми вирішили його вивозити. Мені вдалося частину вивезти. На той момент я не знав, куди переїжджаю і що буде. В телефонному режимі домовлявся, куди можна все перевезти, де зняти цех. Це було важко: треба було все розібрати, повантажити, вирішити транспортні питання. Ми тоді ще й під обстріл попали.
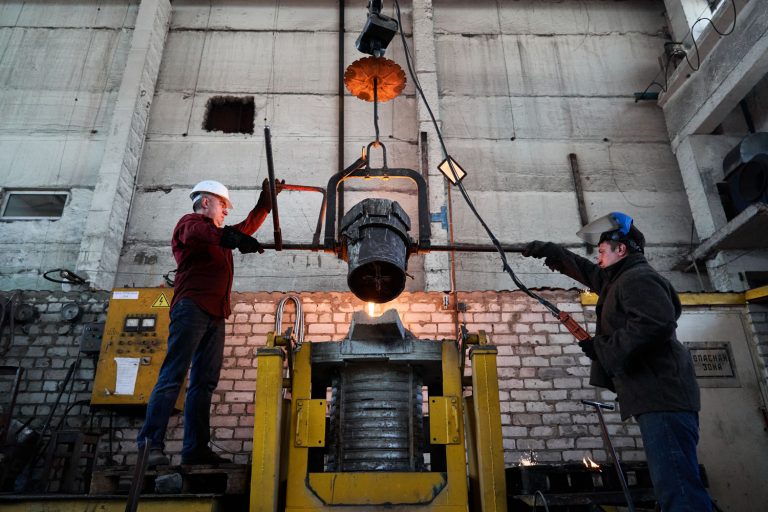
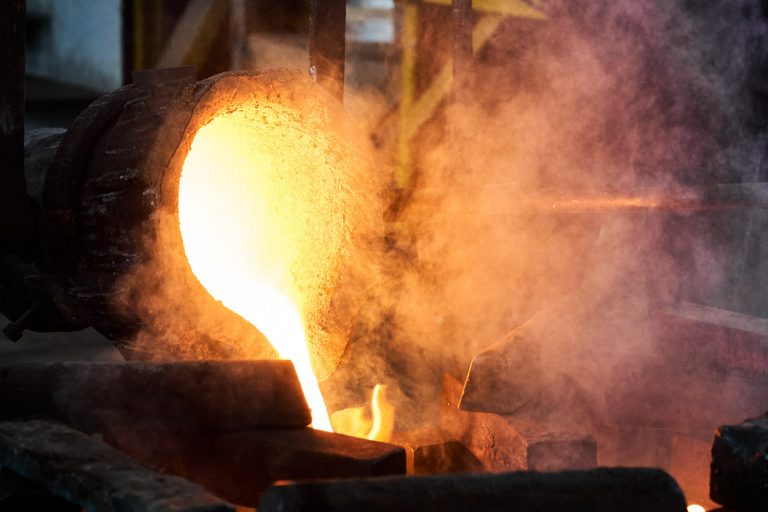
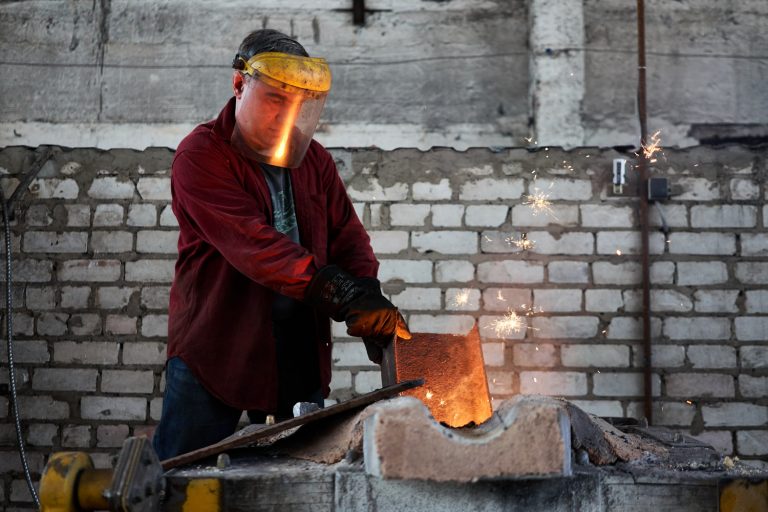
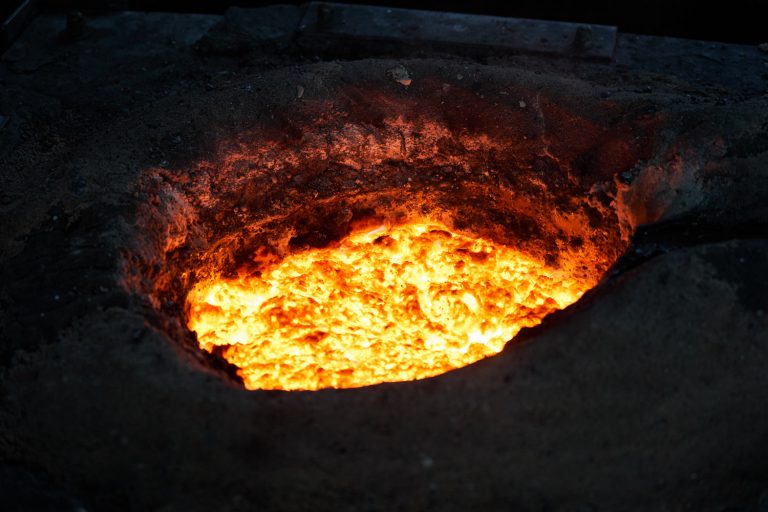
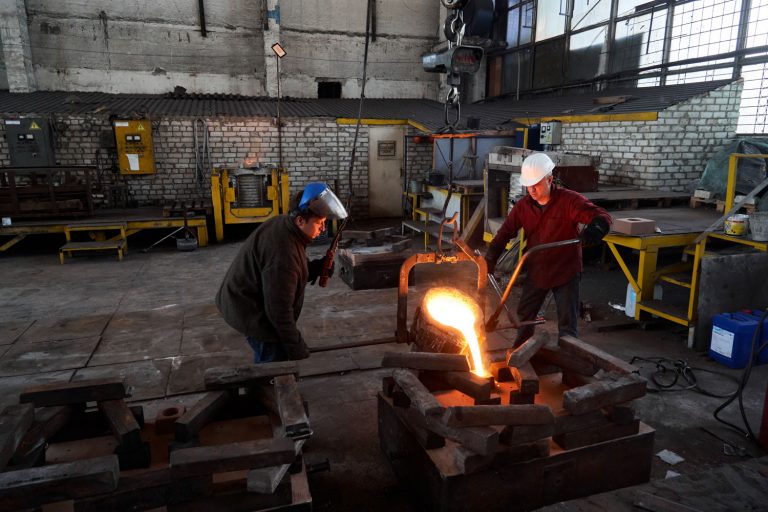
слайдшоу
Дмитро своїми силами перевіз частину обладнання та працівників до Вінниці, а згодом компанія переїхала до Чернігова, де, за словами Дмитра, були вигідніші умови купівлі приміщення під цех. У 2015 році виробництво відновили:
— Частину персоналу я перевіз із Луганська, орендували для них гуртожиток. Виготовляли найпростіші речі — буржуйки для військових, які на той час не мали опалення. Щось серйозне не могли без лабораторного обладнання. Першою допомогою від ЄС була Програма з компенсації створення робочих місць для переселенців, і вони допомогли нам купити сучасну лабораторію, відшкодувавши половину її вартості.
Відтак компанія розпочала виготовляти спеціальні антифрикційні сплави з металобрухту, повернулася до виробництва підшипників та підписала контракти із партнерами з Угорщини та Чехії. Також «Символ» намагається підтримувати наукові розробки в Україні, тому співпрацює з Інститутом проблем матеріалознавства НАН України та Науково-дослідним інститутом матеріалів та сплавів, створеним за їхньої ініціативи.
Брухт
Непридатні для прямого використання вироби з чорних або кольорових металів чи їхніх сплавів, а також браковані деталі чи залишки від виробництва та металообробки.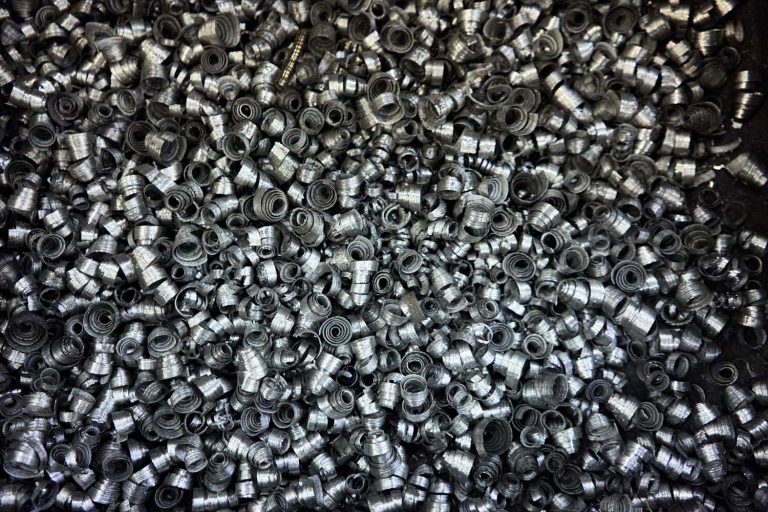
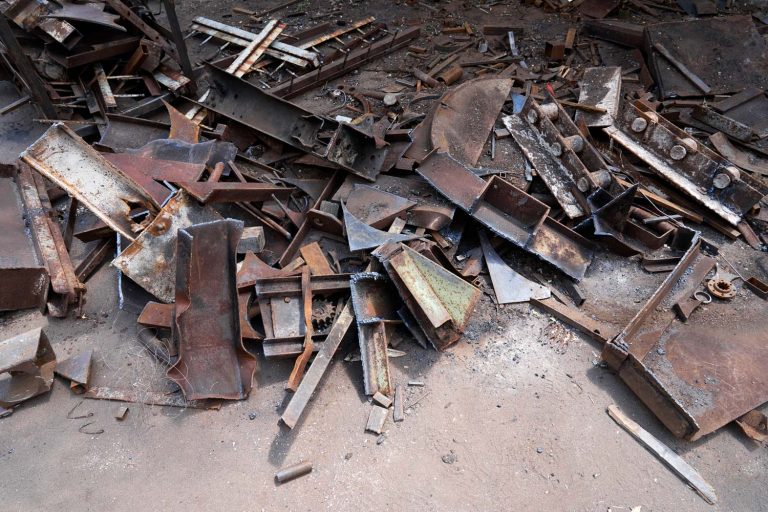
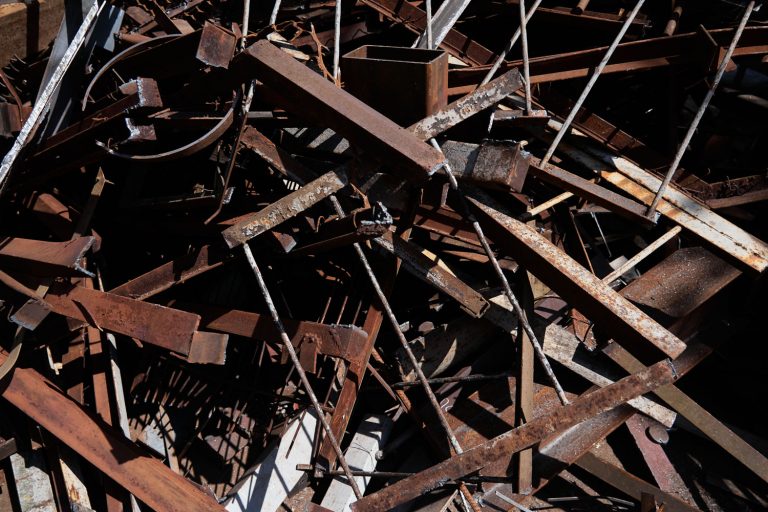
слайдшоу
Для переходу на масове виробництво, каже Дмитро Акішин, поки не вистачає потужностей, тому робота зараз спрямована на внутрішній ринок — виробництво підшипників ковзання для України.
У 2018 році Компанія «Символ» отримала грант у рамках проєкту «Кліматичні інноваційні ваучери», реалізованого ГО Greencubator за сприяння Європейського банку реконструкції й розвитку та Європейського Союзу. Завдяки фінансовій підтримці вони сертифікували виробництво та отримали європейські патенти. Також компанія підписала договори з виробничими партнерами в ЄС. За словами Дмитра, компанія планує залучити інвестиції на закупівлю обладнання для серійного виробництва.
— В Україні є дуже багато умов для розвитку: наукові центри, унікальні професіонали, комбінати, виробничі об’єкти та багато ресурсу. Для розвитку потрібні інвестиції та ефективне обладнання.
Технологія виробництва підшипників з брухту значно скорочує викиди СО2 в атмосферу порівняно з виробництвом із інших сплавів (0,7 кг СО2 на кг сировини, що у 5 разів менше ніж при виробництві деталей з бронзи та у 16 разів менше ніж при використанні сплавів алюмінію).
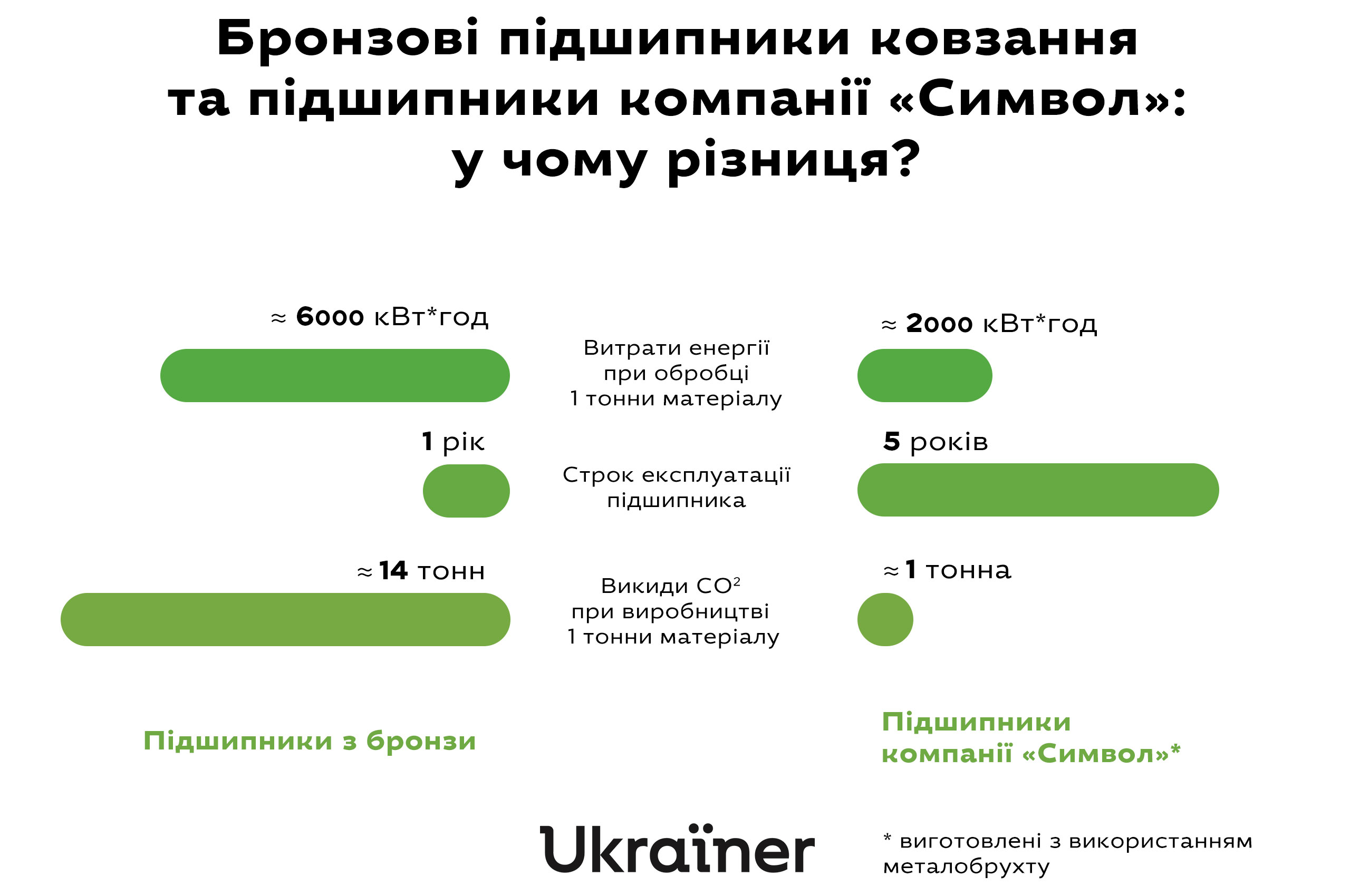
Компанія використовує для виробництва металобрухт, який продукують українські підприємства. «Символ» купує та переробляє старі вироби та обладнання, таким чином утилізуючи їх:
— Наприклад, в Укрзалізниці ми купуємо старі рейки й переплавляємо їх. У Чернігові є машинобудівне підприємство, у якого залишаються відходи. Ми, як ливарне підприємство, ці відходи купуємо та виготовляємо з них деталі.
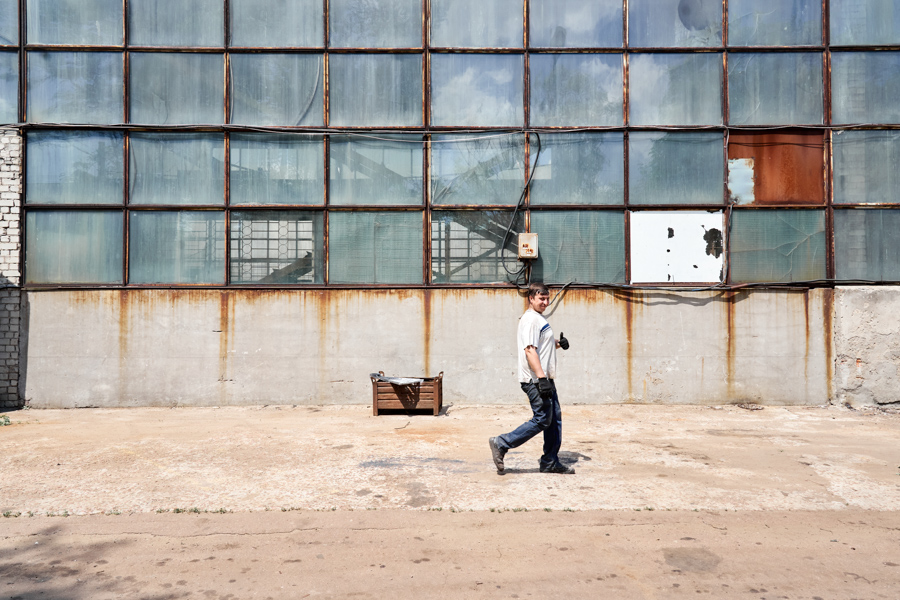
Металобрухт є сировиною для ливарного та металургійного виробництва. Дмитро Акішин каже, що українські компанії просто не в змозі конкурувати в обсягах виробництва з турецькими чи китайськими металургійними підприємствами, бо в тих є велика підтримка від держави. Наприклад, низька вартість електроенергії для промислових виробників. Українські компанії з високою вартістю електрики та кредитів не мають можливості зайняти масовий сегмент на світовому ринку, каже Дмитро:
— Дуже багато нашого металобрухту йде на експорт. Наприклад, десь 70% сировини йде в Китай. Туреччина також купує в нас брухт, а потім масово привозить сюди запчастини за такою ціною, що наш сегмент не може конкурувати. Ми віддаємо сировину, яку можна переробляти та використовувати всередині країни. Конкурувати можна лише якимись інноваціями.
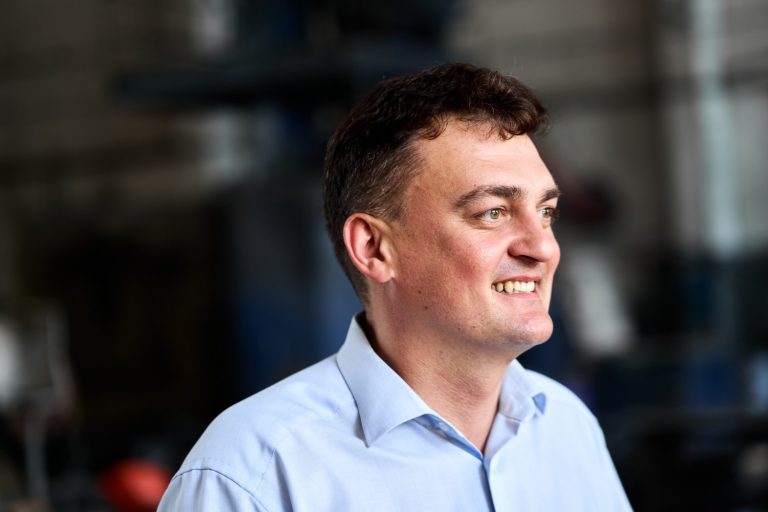
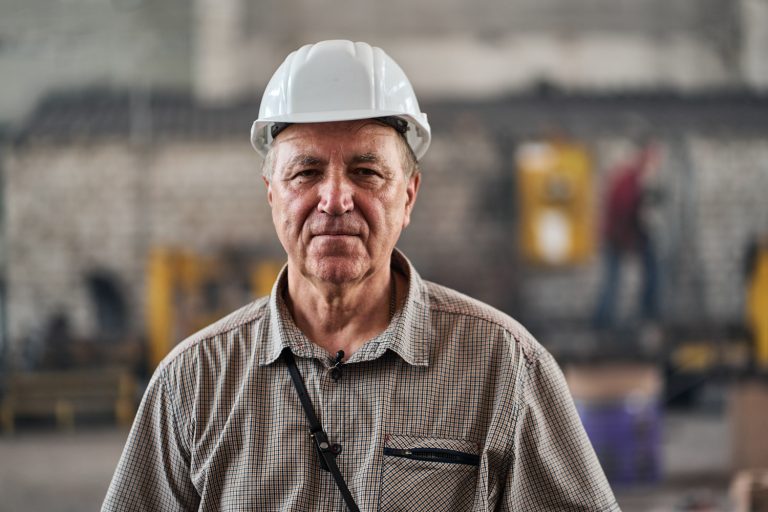
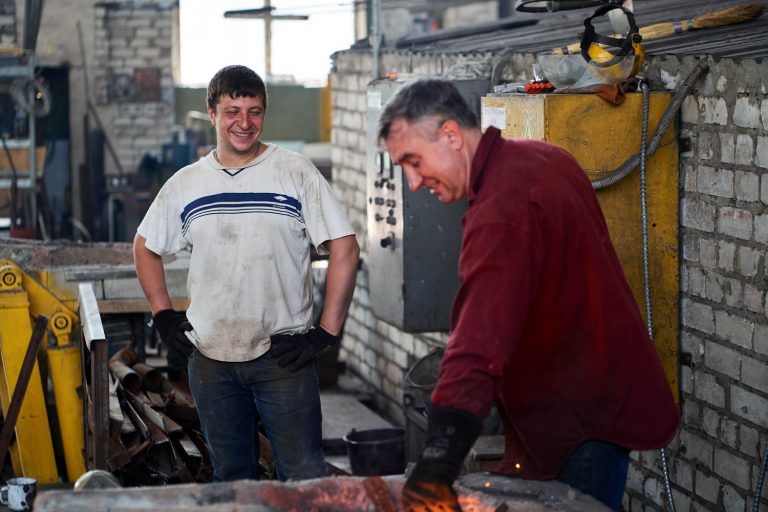
слайдшоу
Підшипники ковзання з чорного металобрухту мають учетверо довший термін придатності, ніж такі ж вироби з бронзи. І коштують вони на 70-80% дешевше, бо заощаджують сировину та електроенергію:
— Під час створення нашого сплаву використовується металобрухт і невелика кількість добавок. А під час виробництва бронзи використовують багато шкідливих речовин, які впливають на навколишнє середовище. Якщо проєктується якась велика машина — гідроелектростанція, наприклад — то замовлення на підшипники може тривати до року. А в нас може бути у 2-3 рази менше по термінах.
«Червона хвиля». Друкувати металом
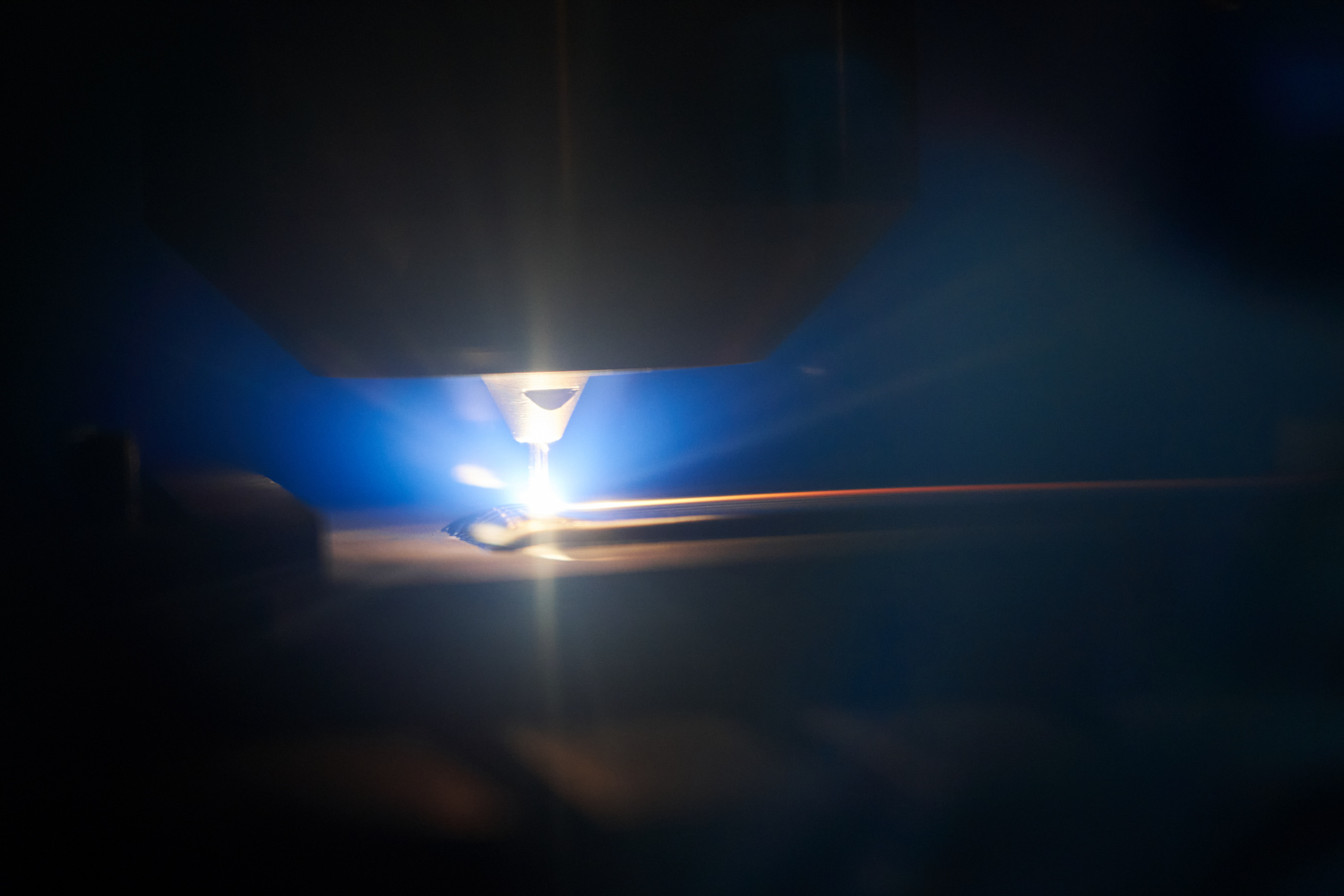
3D-друк давно активно використовують у легкій промисловості, дизайні, архітектурі, медицині, будівництві та в інших галузях. За допомогою 3D-принтера можна створювати різні деталі та об’єкти. Щоб надрукувати фізичний об’єкт, потрібно створити його цифрову 3D-модель засобами комп’ютерного моделювання чи відсканувавши 3D-сканером реальний об’єкт. Таку модель можна зберегти на комп’ютері в спеціальному форматі і в потрібний момент передати на 3D-принтер на друк. Тоді принтер опрацює файл та розпочне процес відтворення об’єкту: друкуюча частина принтера нанесе перший шар матеріалу, розплавить його або випече лазером (в залежності від способу друку). Далі друк буде безперервно повторюватися шарами, ніби накладатиметься один на одний, аж поки не з’явиться фізична копія тривимірної моделі потрібного розміру.
Українські розробники, що працюють у сфері металообробки, застосували технологію 3D-друку для створення міцних деталей з титану, які нині використовуються для космічної та авіаційної галузей у низці країн світу.
Команда підприємства «Червона хвиля» розробила унікальну установку, яка друкує деталі з титанового дроту. Технологія називається xBeam 3D Metal Printing та, за словами розробників, є дешевшою, безпечнішою та швидшою, ніж традиційні методи виготовлення титанових виробів, як от фрезерування.
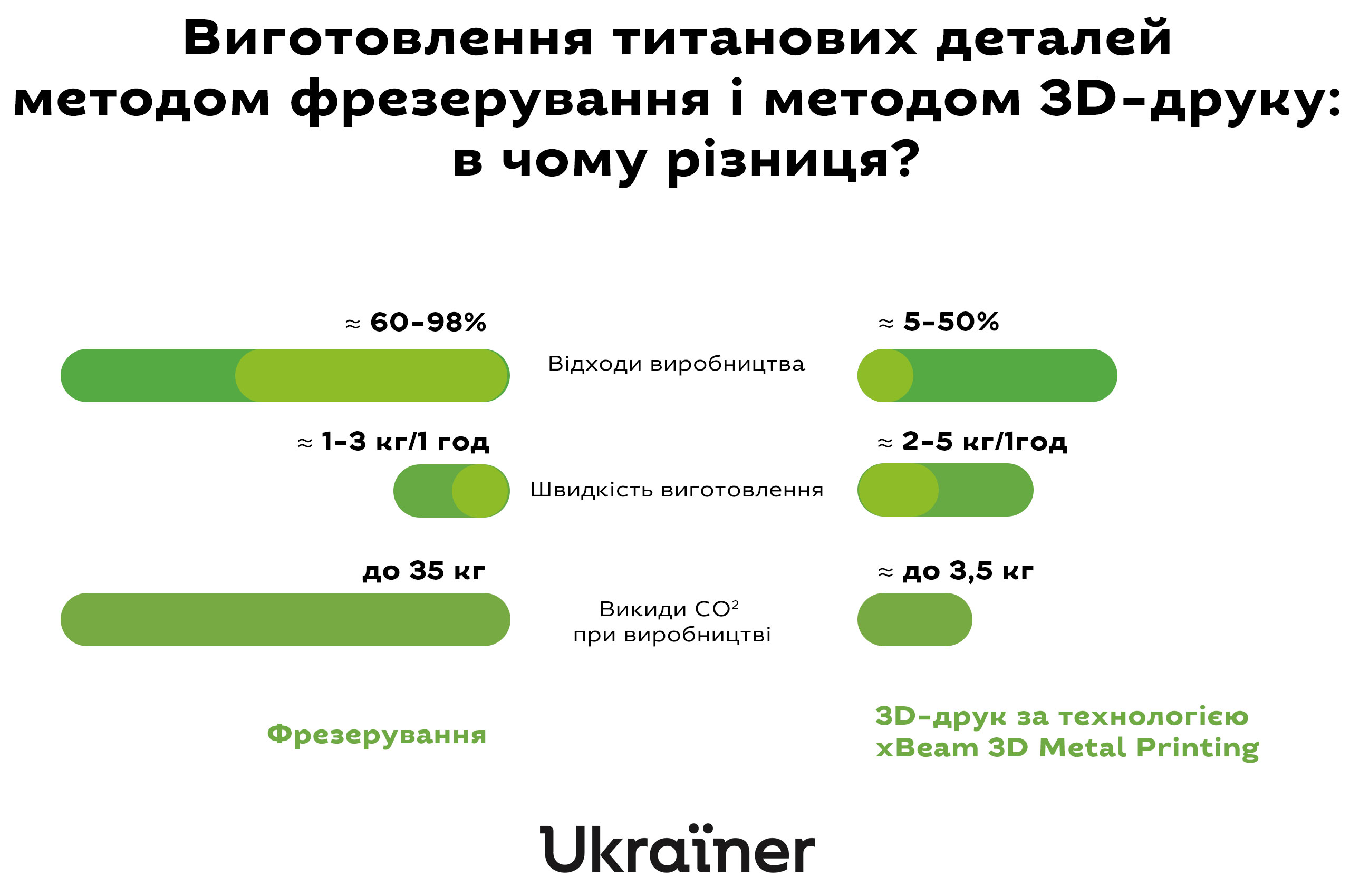
Також, за словами співзасновника компанії Дмитра Ковальчука, друк саме розплавленим дротом, а не титановим порошком (порошковий спосіб 3D-друку), є дешевшою та простішою в експлуатації технологією.
Порошкові технології друку металом, за словами Дмитра, є застарілими й використовуються зараз переважно в медицині. У широке застосування такі технології вже не потрапляють через високу собівартість порошків і, відповідно, виробів із них, а також через великий відсоток відходів при такому способі друку.
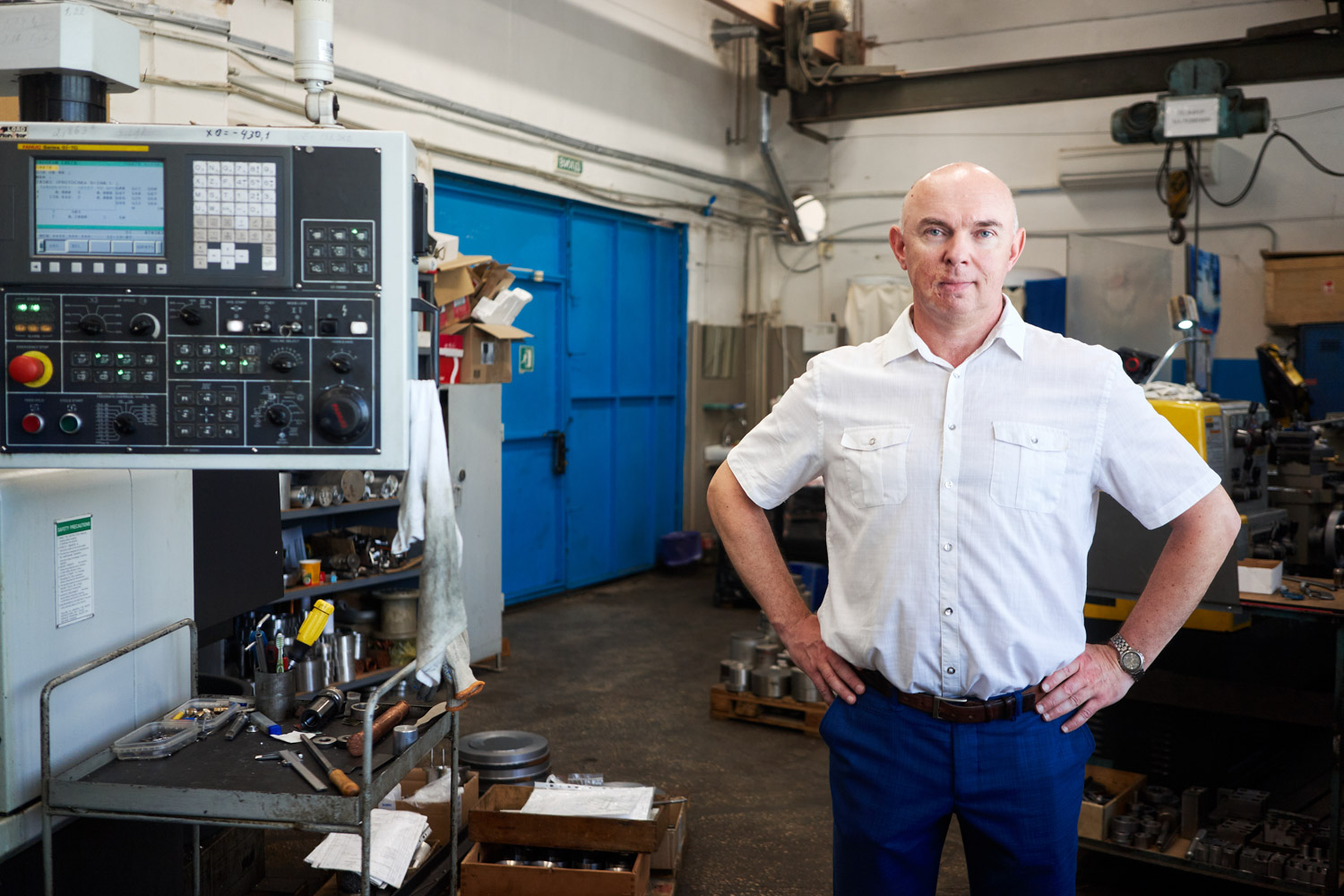
— Порошки дуже нетехнологічні, бо дуже дрібні. Це як пил, вони кругом розсипаються. А порошки активних металів, таких, як титан, ще й пожежо- та вибухонебезпечні. Тобто вони вимагають спеціальних заходів безпеки, спеціальних приміщень, спеціальних навичок, досвіду.
Титан відкрили ще у XVIII ст. та активно використовувати почали лише з другої половини ХХ ст. Цей метал ще називають «летючим». Через надзвичайну міцність, стійкість до корозії та суттєво меншу, порівняно з іншими металами, масу титан часто використовують у виробництві ключових деталей там де критично важливою є вага і надійність виробу: наприклад, для виготовлення деталей літаків, ракет, турбін чи спортивних болідів.
«Червона хвиля» працює з титаном вже понад 20 років. Заснована в 1997 році, компанія спершу виробляла титанові злитки з переробленого металобрухту і постачала їх на світовий ринок. Використання вторинної сировини значно здешевлювало зазвичай дуже дорогі титанові вироби без втрати якості.
— В Україні металобрухту було дуже багато, бо в 90-ті роки, після розпаду Радянського Союзу, багато підприємств просто вирізали. Брухт кольорових металів експортувався за кордон фактично за безцінь. А ми, ознайомившись з потребами титанової індустрії і маючи технологію електронно-променевого переплаву, розробили методику утилізації титанового брухту й виготовлення титанових злитків.
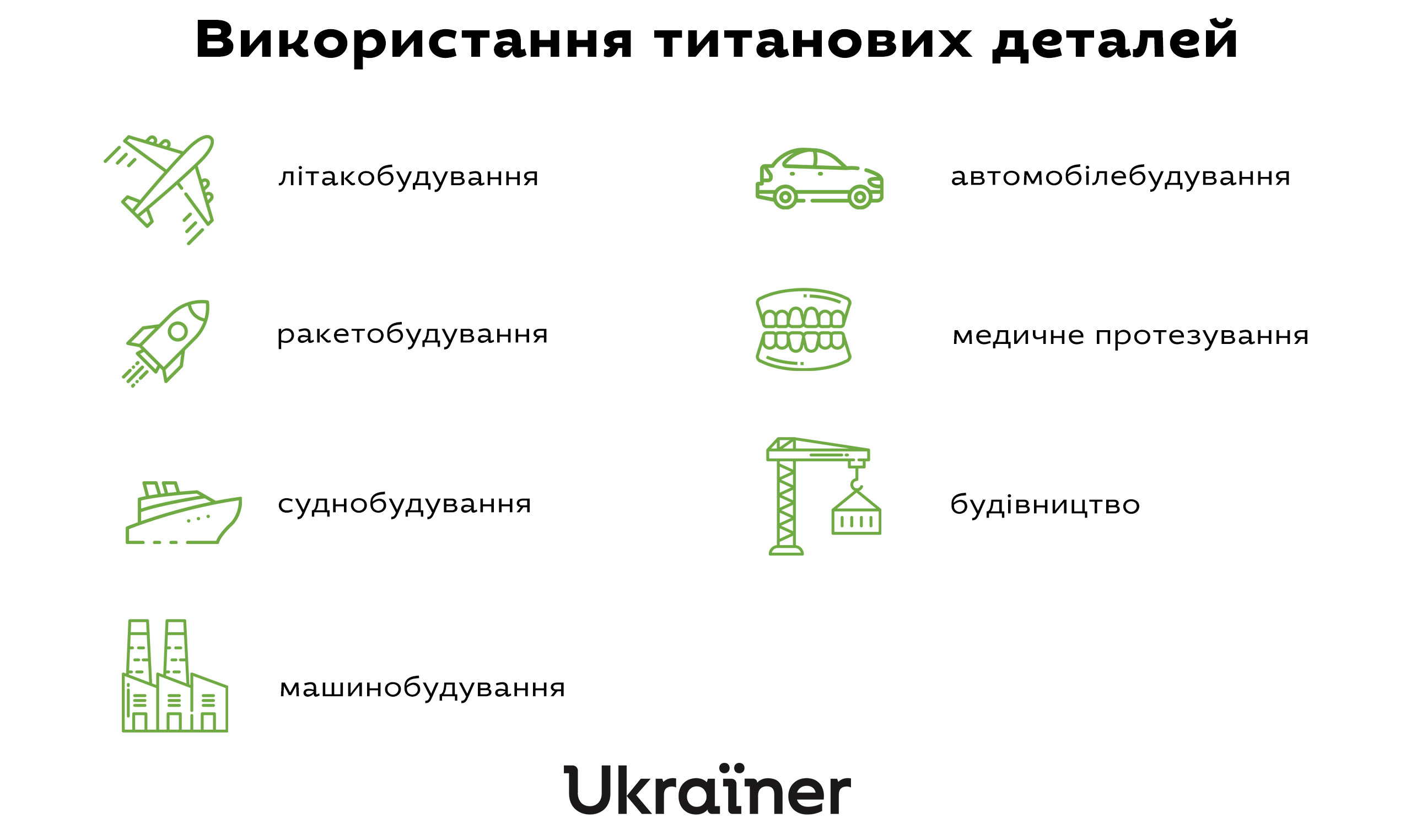
Дмитро Ковальчук розповідає, що саме команді «Червоної хвилі» належить ідея постачати весь металобрухт на переробку. Ще у 1996 році, відвідавши американські титанові підприємства, Дмитро побачив, що з продукції, яку в Україні продавали, можна виплавляти якісні титанові злитки. Тоді з партнерами з інституту Патона вони вирішили спробувати використовувати металобрухт у виробництві:
— У результаті ми вийшли на світовий ринок буквально через рік-два. На той час з фантастично дешевою продукцією, яка була якісною. Серед наших покупців були підприємства Америки, Китаю, Росії. І дійшло до того, що на якомусь етапі ми почали імпортувати брухт в Україну. Коли з України брухт та метал вивозився ешелонами, ми купували брухт в Німеччині і платити ціну більше. Ми розвернули ці потоки. Ми нарощували об’єми виробництва і поступово стали дуже помітними гравцями на світовому ринку.
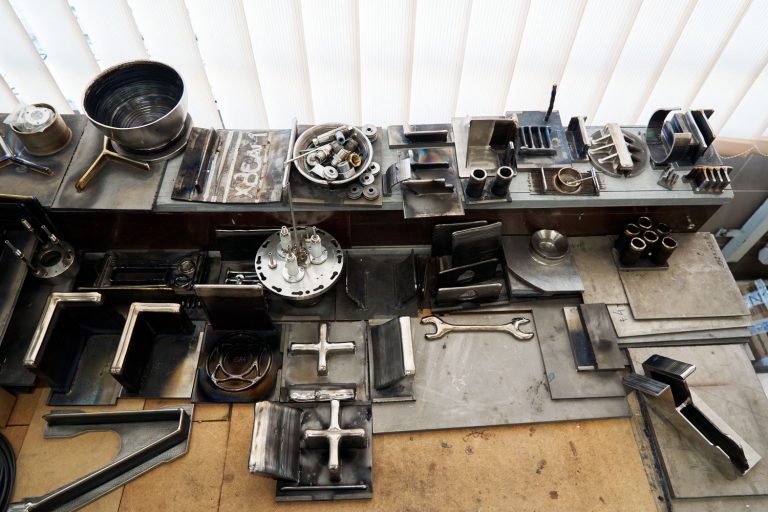
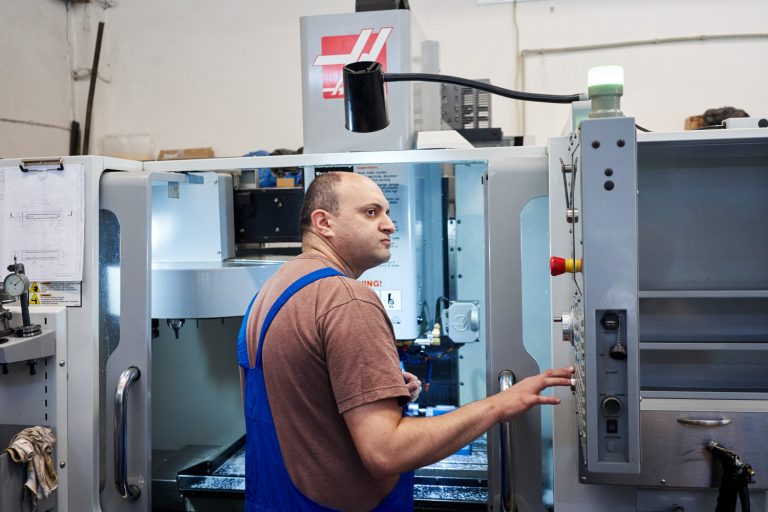
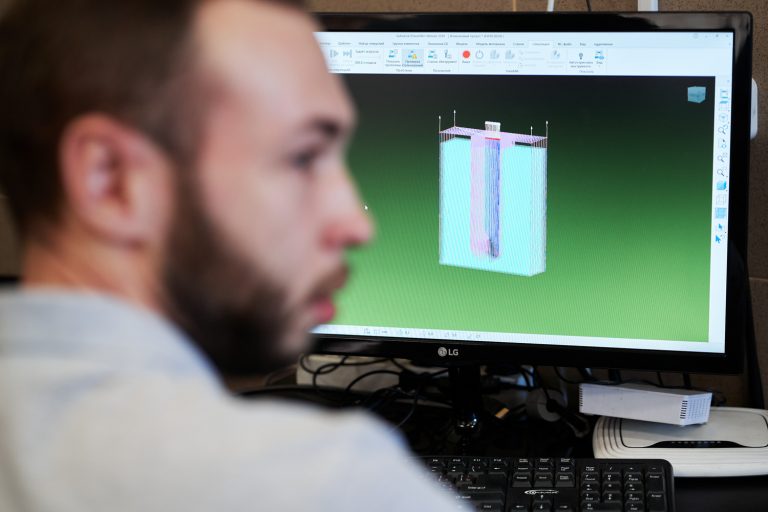
слайдшоу
Попри свою широку розповсюдженість у природі, титан все ще вважається екзотичним і дорогим металом. Він стійкий до високих температур (температура плавлення титану — приблизно 1700°С). Механічна обробка (фрезерування) титанових злитків також потребує значних ресурсів та дорогого обладнання. І на додачу титанові відходи — стружка і брухт — важко утилізуються, тому технології, де відходи виробництва мінімізуються, є оптимальним рішенням.
— Титан — дуже цікавий метал. Я займаюсь титаном вже більше тридцяти років. У нього є унікальний набір характеристик і властивостей. Він одночасно і міцніший багатьох сталей, і майже вдвічі легший. Тобто ви можете ту саму деталь з тими самими навантаженнями зробити вдвічі легшою.
«Червона хвиля» подавала заявки на низку програм із підтримки інноваційних зелених рішень у виробництві. Команда отримала грант від програми «Горизонт 2020», а в 2018 році — фінансування у 50 тис. євро в межах проєкту «Кліматичні Інноваційні Ваучери», реалізованого ГО Greencubator за сприяння Європейського банку реконструкції й розвитку та Європейського Союзу. Інноваційний ваучер допоміг компанії розробити програмне забезпечення для автоматизації процесу друку деталей та інтеграції з провідними програмами для інженерії та проектування (CAD-системами). Це зменшило кількість помилок друку, підвищило вихід якісних деталей і покращило якість їхніх поверхонь, зменшуючи, відповідно, потребу фінальної обробки.
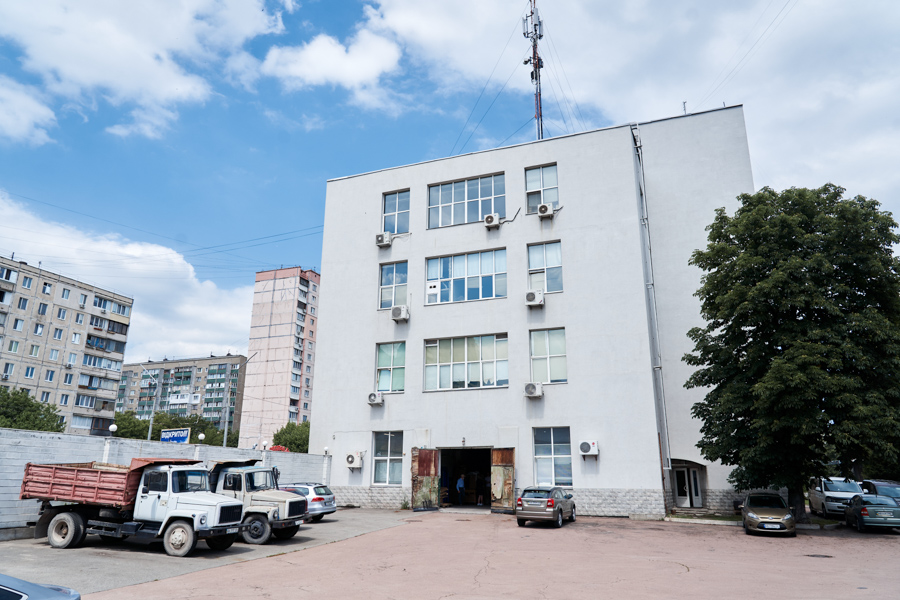
— Ми працюємо над збереженням ресурсів. І це важливо для всього світу. Наприклад, в Україні вже друкують порошками за допомогою лазера. Знаю, що в Одесі є компанія, яка розробила технологію друку керамікою. Було б чудово, якби в них все було окей. І в Україні була б своя школа друку. Тому підтримка таких зелених проєктів — це приклад взаємодії, бо користь отримають всі сторони.
2019 року систему друку компанії «Червона хвиля» придбав Британський дослідницький інститут зварювання для аерокосмічної галузі Великобританії.
— Зараз у нас три контракти діючі. Один — у Великій Британії, в Кембриджі, i два контракти з китайськими замовниками. Всіх їх поєднує те, що їхнє основне призначення — це аерокосмічна галузь. Це дослідницькі організації, які працюють в інтересах аерокосмічної галузі.
Технологія хBeam 3D Metal Printing. Початок
Дмитро Ковальчук закінчив факультет аерофізики та космічних досліджень Московського фізико-технічного інституту, який за радянських часів співпрацював із Інститутом електрозварювання імені Патона НАН України.
— У нас була виїзна схема навчання. Ми чотири роки в Москві вивчали загальні предмети, здавали державні іспити і потім, на 5-6-й курс, переїжджали у Київ, де нас прикріпляли до конкретних відділів Інституту Патона, і ми брали участь в наукових дослідженнях.
На базі Київського політехнічного інституту та Інституту імені Патона, де після закінчення навчання Дмитро залишився працювати, з кінця 1960-х років діяла потужна наукова школа з розробки й створення електронно-променевого обладнання. Тут виготовляли плавильні печі, зварювальні установки і в тому числі електронні гармати, виробляти деталі до яких і почала 2005 року «Червона хвиля».
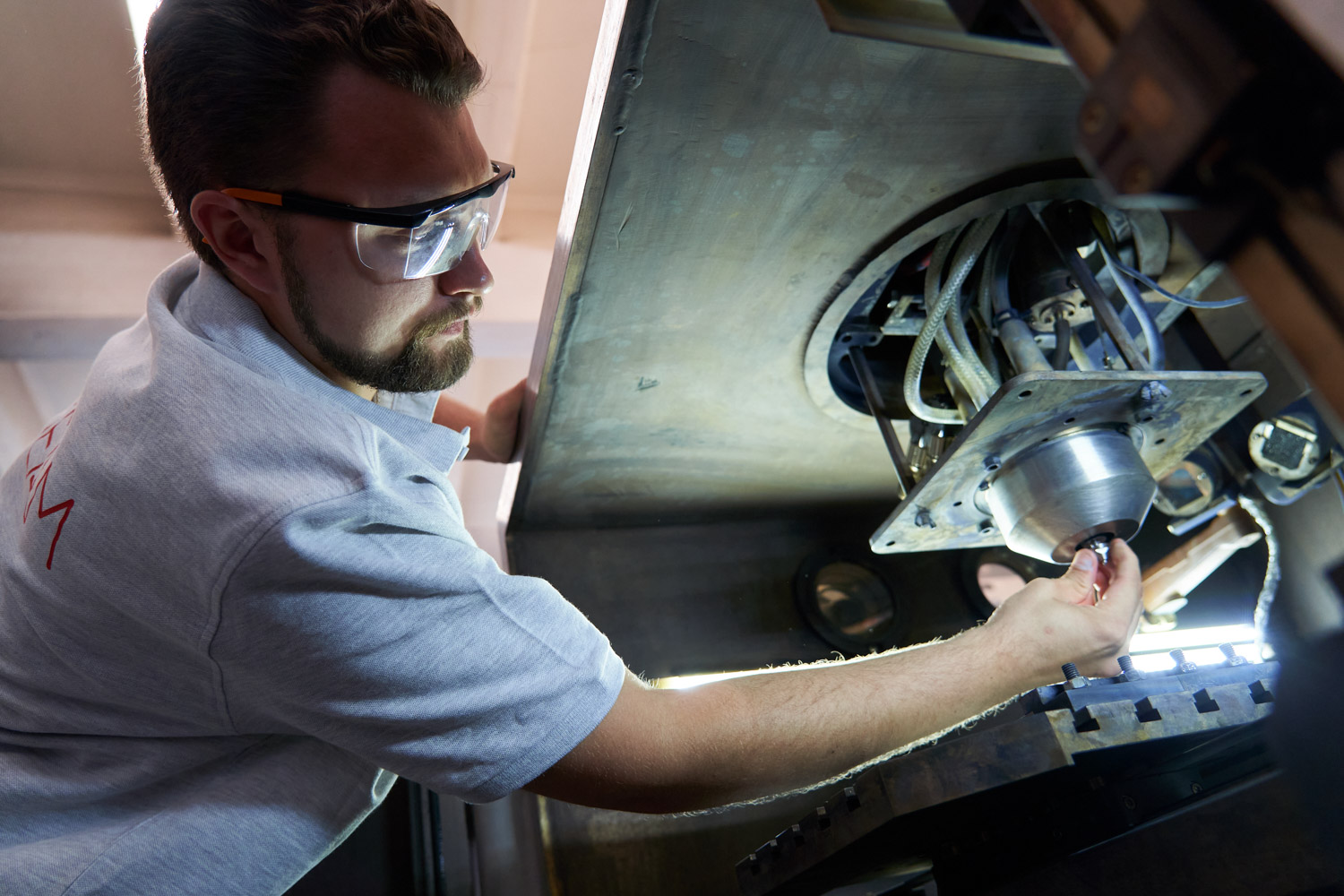
Електронні гармати газорозрядного типу «Червона хвиля» створила разом із науковцями Київського політеху. Такі гармати використовуються для імпульсного нанесення багатокомпонентних та складних металевих покриттів. Сьогодні українськими електронними гарматами користуються в США, Китаї, Японії та країнах Європейського Союзу.
Електронна гармата або електронно-оптична система (ЕОС)
Вузол електронно-променевого приладу, призначений для формування спрямованого пучка електронів.— З самої назви випливає, що електронно-променева гармата — це пристрій, який, так би мовити, стріляє електронами. Це пристрій, який формує електронний промінь — пучок електронів, які вилітають із гармати з величезною швидкістю. Вони прискорюються високою напругою, яка подається на катод (електрод приладу, приєднаний до негативного полюса джерела струму. — ред.). Велика кількість електронів, зібраних в промінь, несе з собою шалену енергію.
Високопотужна електронна гармата, за словами Дмитра Ковальчука, може розплавляти до 8-9 кг титанового дроту на годину.
Технології, над якими «Червона хвиля» працювала до 2014 року, мали подвійне призначення. Наприклад, вироблені деталі можна було використати як для цивільного літака, так і для військового. Тому деякі країни застосовували обмеження на експорт:
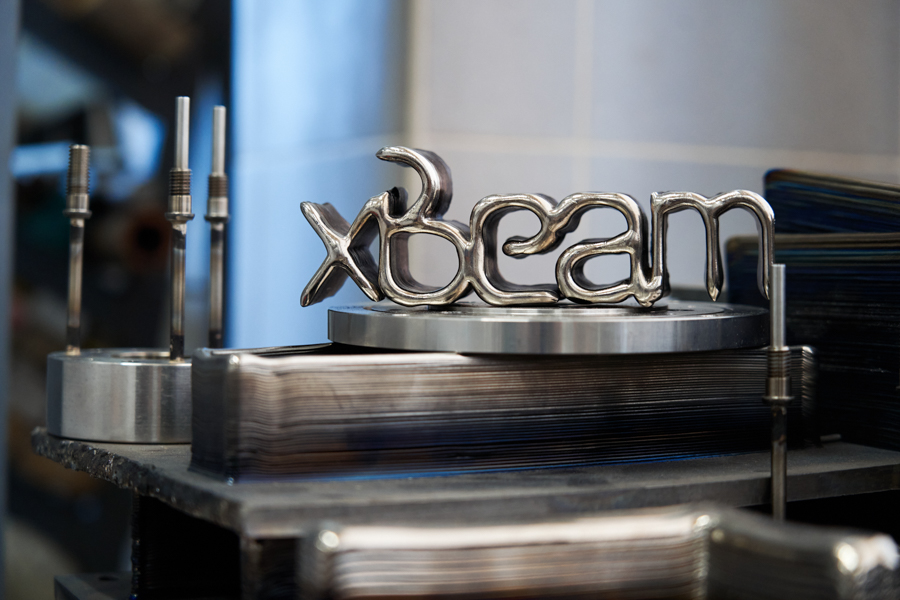
— Це вже питання, в чиї руки це попаде (обладнання. — ред.) і хто як його використає. Наприклад, коли в нас була замовником американська компанія, яка знала, що ми постачали обладнання і в Росію, то в них були певні застереження, тому наші можливості були обмежені на той час. А 3D-технології не є технологіями подвійного призначення, тому тут все значно простіше, без обмежень.
З 2014 року компанія зосередилася на розробці власної технології тривимірного друку виробів з металевого дроту:
— Одного разу, коли я відвідував нашого замовника електронних гармат в Китаї, вони мені показали технологію 3D-друку, яку вони розробляли на базі іншого обладнання, і запитали, чи можемо ми ефективність своїх гармат застосувати тут. З цього розпочалася наша мандрівка в 3D-друк. Тоді, шість років тому, я був вражений, що майже ніхто не займався друком із використанням дроту.
Та якщо ринок виплавки металу в Україні та його постачання на той час Дмитро вже вивчив, то на ринку 3D-друку «Червона хвиля» починала роботу майже з нуля.
— Базові інвестори в нас були, звичайно, серед знайомих. Як водиться, ті, хто більше довіряв мені, ніж проєкту. Бо проєкту ще не було, не було прибутків, не було розуміння, як ми будемо виходити на ринок, бо ринок для нас новий, і ми там ніхто. Тому перші наші залучені кошти — це були фактично такі дружні кредити.
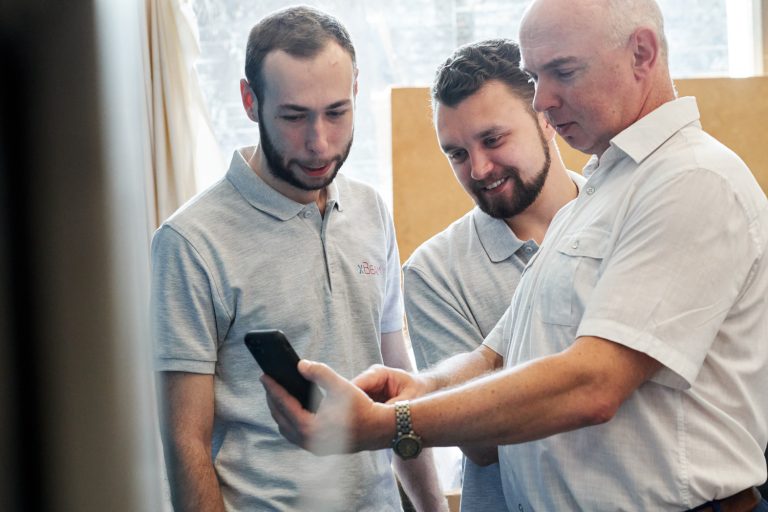
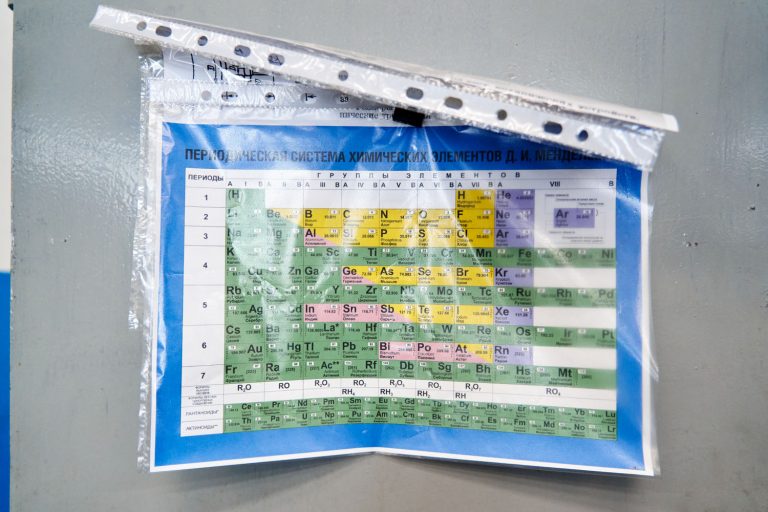
слайдшоу
«Червона хвиля» зараз виробляє три типи систем для 3D-друку титаном. Перша — так звана «лабораторна» система XBeamLab. Це компактна система, яка призначена передусім для проведення експериментів в університетах та для малих виробників, кому треба виготовляти невеликі деталі.
Наступна система — XBeamWorks (в англійській мові works — заводи, виробничі цехи). Це система середнього розміру, деталь з якої органічно можна взяти, перемістити на станок із комп’ютеризованою системою керування для фінальної обробки і отримати вже звідти готову деталь.
Інколи виникає потреба друкувати дуже великі деталі або якоїсь незвичайної конфігурації. XBeam Grand — це загальна назва для всього нестандартного, великого обладнання.
Під час створення титанової деталі способом фрезерування від 60 до 90% металу йде у відходи. Якщо там для виготовлення деталі потрібно, наприклад, 20-30 кг титану, то за технологією xBeam 3D Metal Printing на неї піде лише 3-5 кг. Якщо виробництво 1 кг титану утворює до 35 кг викидів СО2, то 3D-друк зменшує шкідливі викиди в атмосферу приблизно в 10 разів.
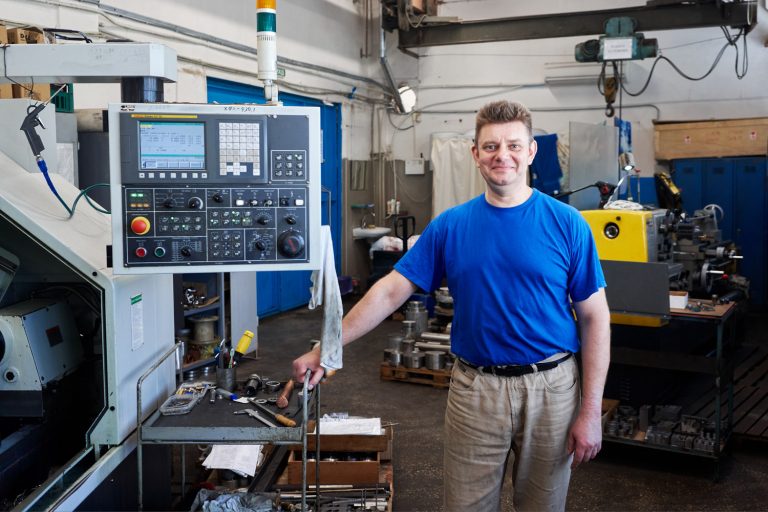
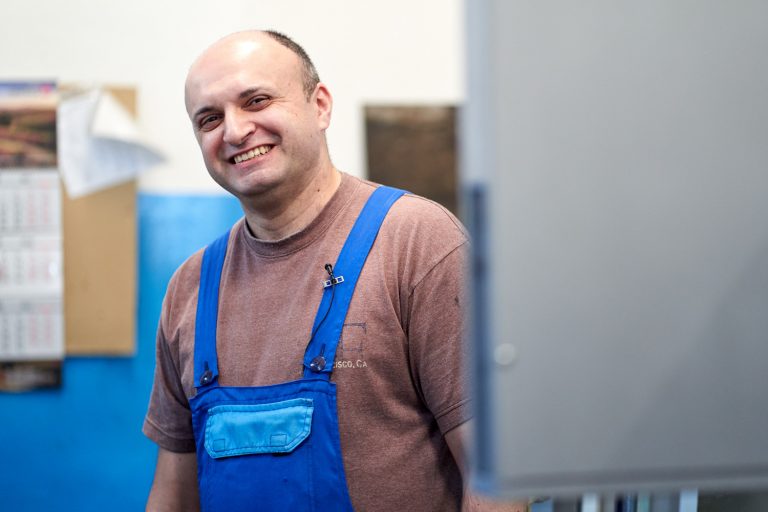
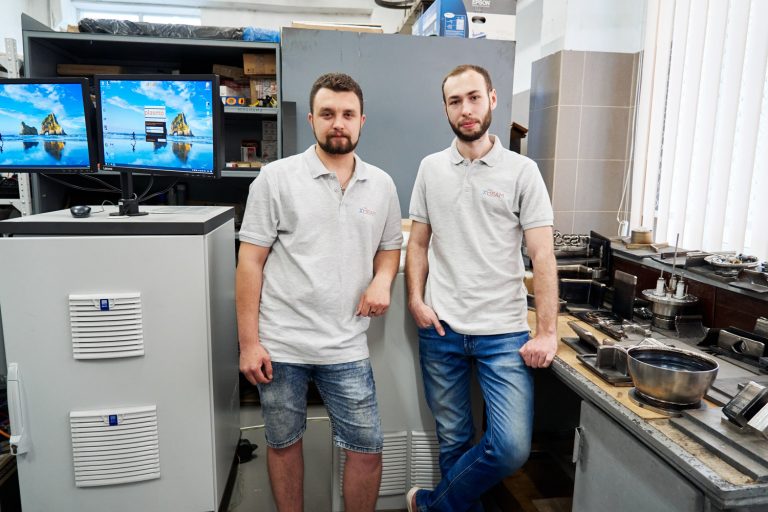
слайдшоу
Розробники 3D-принтера для титану використовують для друку металевий дріт, який плавиться у точці фокусу електронного променю під дією високих температур. І саме з нього принтер формує необхідну деталь. Назва технології xBeam походить від форми самого електронного променю, який нагадує літеру Х.
— Ідея виникла як схема на папері, щоб створити прототип, провести певний експеримент, отримати наш перший оцей Х-промінь і надрукувати першу деталь. Трошки менше року знадобилося на те, щоб ми перевірили самі себе і побачили, що це працює.
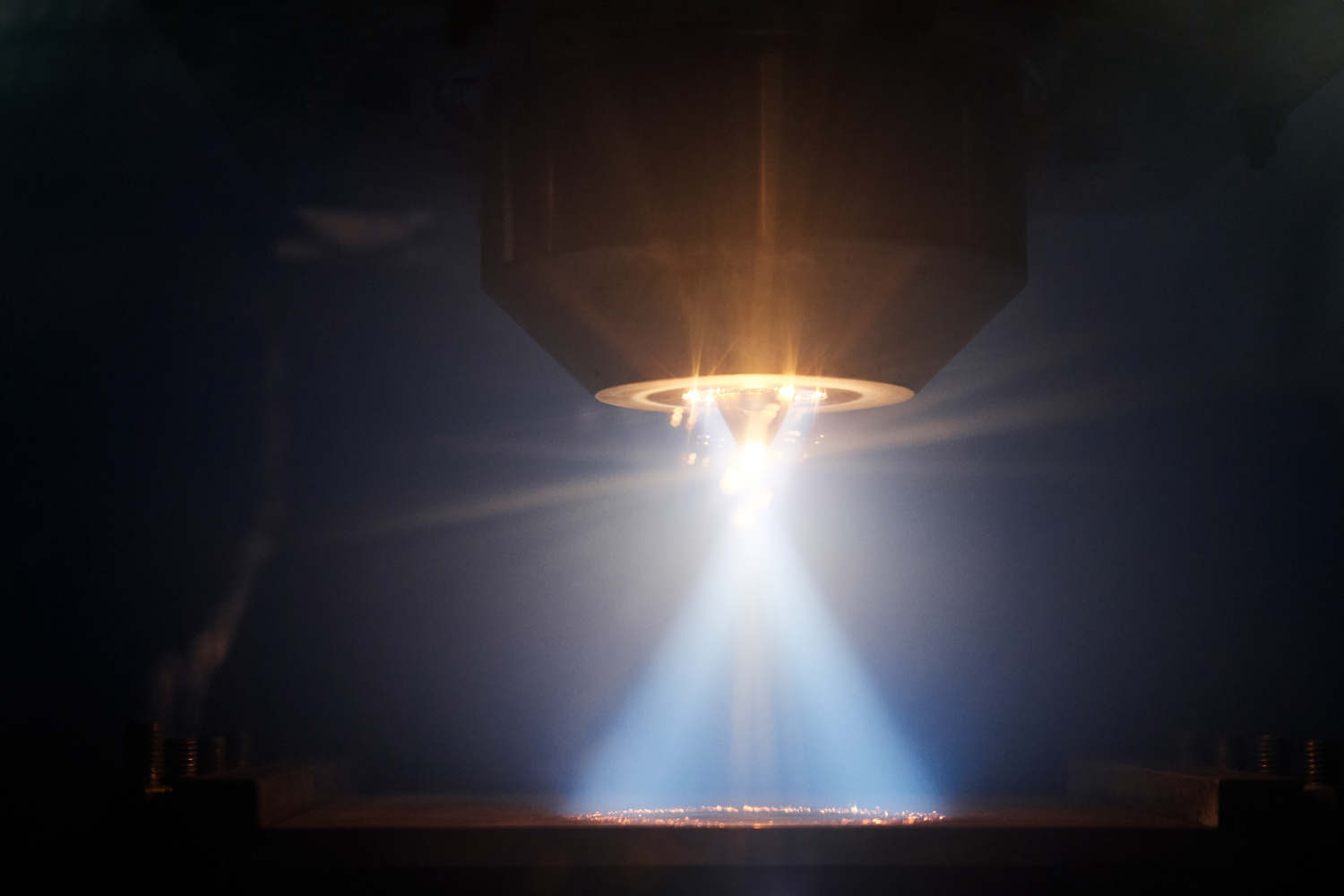
Унікальною особливістю серед інших технологій 3D-друку в компанії називають саме якісний і точний контроль процесів виробництва:
— Наша технологія — це ніби ви видавлюєте зубну пасту на щітку, коли вона дуже просто, контрольовано та рівномірно розтікається на ті поверхні, на які вам треба. І це наша головна критична перевага перед усіма іншими технологіями 3D-друку. Ми додаємо метал дуже контрольованим чином: контролюємо структуру, а отже і якість металів. Та зменшуємо кількість відходів, які утворюються подальшою обробкою.
за підтримки
Greencubator та проєкту «Кліматичні Інноваційні Ваучери», що фінансується Європейським банком реконструкції та розвитку та Європейським Союзом.
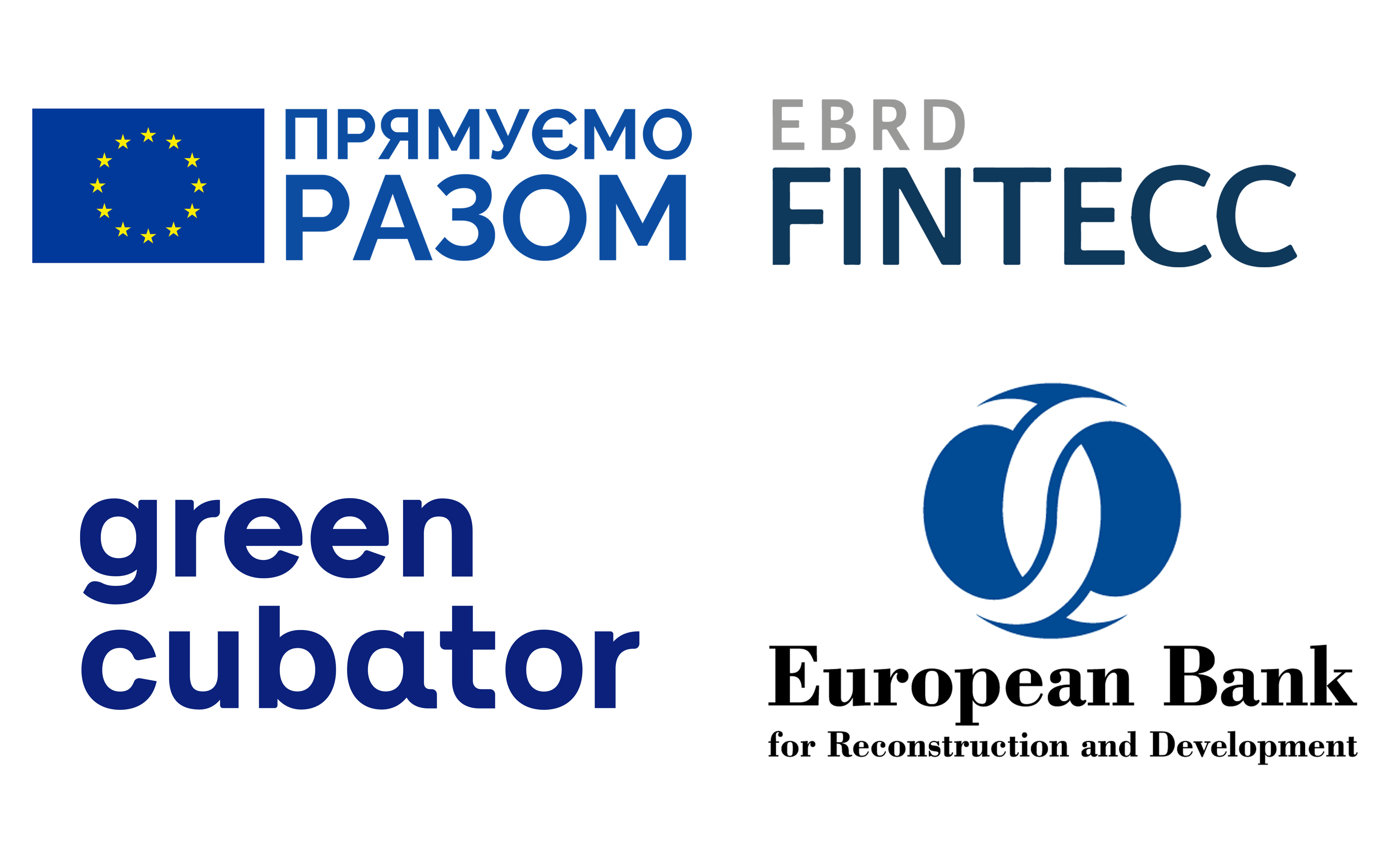